learningallthetime
New member
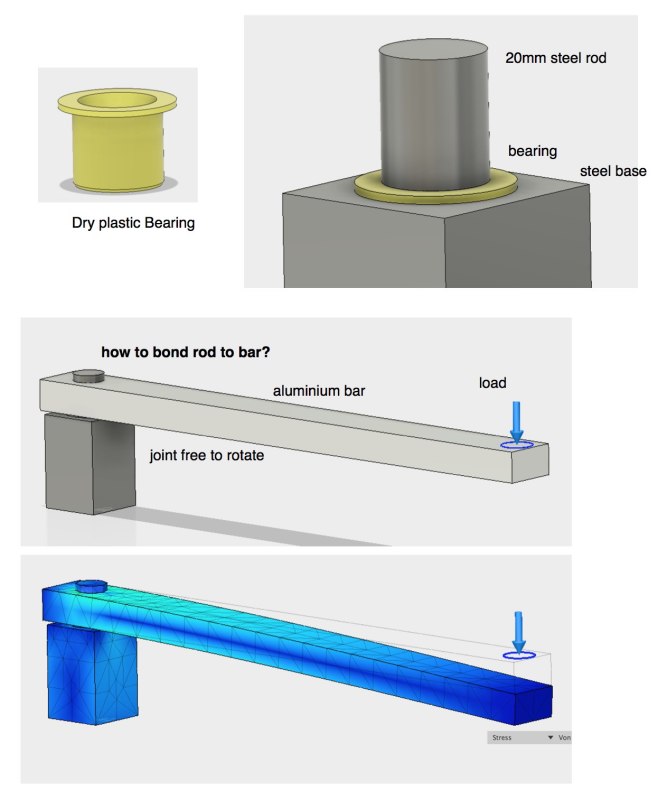
A 20mm steel rod is held vertically by a dry plastic cylindrical bearing such that it can rotate freely in the horizontal plane.
An aluminium bar with a 20mm hole in it is slipped onto the rod and, supported by the bearing below, can rotate freely in the horizontal plane.
The bar must support a load and in order to distribute stresses at the interface between the aluminium bar and the rod it would be best if they were bonded.
What are the options for bonding the aluminium bar and the steel rod? Or other means for reducing stress concentrations under load?
Should I consider mild - rather than hardened - steel and thread the rod?