mechengineer
Mechanical
Currently whatever from client or vendors, all of them use the nozzle external load applying to UG-44 (b).
I think that should not use piping loads (API 660 Table 2 or client specification for nozzle external loads) applying to UG-44 (b)
Piping Loads Apply for Local Stresses Analysis (WRC107/297) and the External Loads on Flange Apply for Re-rating Flange of B16.5 [(UG-44 (b)].
1. The analysis points are different. One is the nozzle neck to shell interface, and another is the sealing joint of a pair of flanges.
2. The loads are different. One is Piping Loads. That is the constrain loads at the point of the nozzle neck to shell interface, which derive from internal pressure, thermal load and boundary constraints on the integrated piping system by Caesar II analysis. The piping loads is applicable for WRC107/297 for local stresses analysis
Another is the External Loads on Flange EXCEPT piping loads derived from internal pressure, thermal load (as we know that the internal pressure and temperature have been already considered in the flange of B16.5). It is applicable for UG-44 (b).
The below sketch may help to understand the external load on nozzle flange.
'W' shall be considered as the external force for the nozzle flange.
'M' shell be considered as the external moment sue to W for the nozzle flange.
3. Solution is that the case need to use UG-44 (b) is rare and most of design may not require UG-44 (b).
I think that should not use piping loads (API 660 Table 2 or client specification for nozzle external loads) applying to UG-44 (b)
Piping Loads Apply for Local Stresses Analysis (WRC107/297) and the External Loads on Flange Apply for Re-rating Flange of B16.5 [(UG-44 (b)].
1. The analysis points are different. One is the nozzle neck to shell interface, and another is the sealing joint of a pair of flanges.
2. The loads are different. One is Piping Loads. That is the constrain loads at the point of the nozzle neck to shell interface, which derive from internal pressure, thermal load and boundary constraints on the integrated piping system by Caesar II analysis. The piping loads is applicable for WRC107/297 for local stresses analysis
Another is the External Loads on Flange EXCEPT piping loads derived from internal pressure, thermal load (as we know that the internal pressure and temperature have been already considered in the flange of B16.5). It is applicable for UG-44 (b).
The below sketch may help to understand the external load on nozzle flange.
'W' shall be considered as the external force for the nozzle flange.
'M' shell be considered as the external moment sue to W for the nozzle flange.
3. Solution is that the case need to use UG-44 (b) is rare and most of design may not require UG-44 (b).
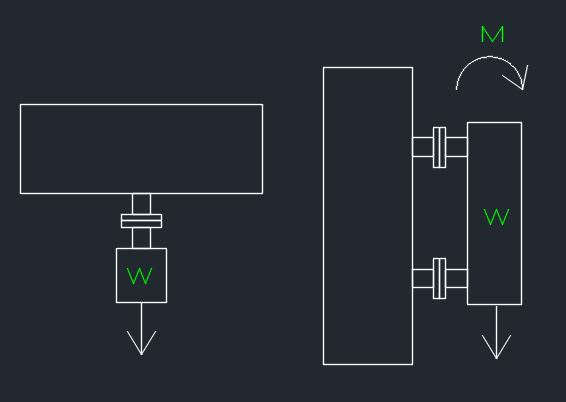