engineerfin
Automotive
- Feb 22, 2015
- 62
In this example, there are a couple of ways of completing the task of replacing the bearing in the field. The factory does not recommend the field operation, they recommend removing the control arm and use a press (major job and super time consuming). The question is which field method would be the best. The press fit between the bearing and spindle and bearing and hub is .001+
1. Freeze spindle (in refrigferator 0-10F) - heat bearing at 200F in oven - slide bearing onto spijndle. Since these parts are small and removable a press could be used. Question would heat be bad for the bearing. Then as an assembly, freeze spindle and bearing - heat control arm housing and drive spindle/bearing into housing. - Question would the driving force from a hammer damage the bearing.
(note:spindle is not long enough to to pulled thru via threads and a nut.
2. Freeze bearing (I have noticed moisture inside bearings when doing this even is bearing is in a sealed bag. could this moisture cause failure down the road) - heat housing and install bearing.
Here is the problem with this method - Freeze the spindle but what do you do with the bearing? cant really heat it.
Good thing about this method is the bearing can be pressed in using a ball joint. Spindle is too large for a too like that.
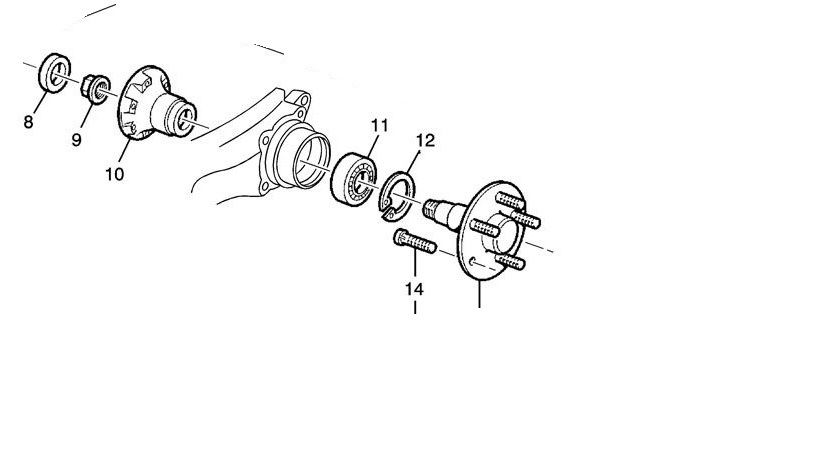
1. Freeze spindle (in refrigferator 0-10F) - heat bearing at 200F in oven - slide bearing onto spijndle. Since these parts are small and removable a press could be used. Question would heat be bad for the bearing. Then as an assembly, freeze spindle and bearing - heat control arm housing and drive spindle/bearing into housing. - Question would the driving force from a hammer damage the bearing.
(note:spindle is not long enough to to pulled thru via threads and a nut.
2. Freeze bearing (I have noticed moisture inside bearings when doing this even is bearing is in a sealed bag. could this moisture cause failure down the road) - heat housing and install bearing.
Here is the problem with this method - Freeze the spindle but what do you do with the bearing? cant really heat it.
Good thing about this method is the bearing can be pressed in using a ball joint. Spindle is too large for a too like that.
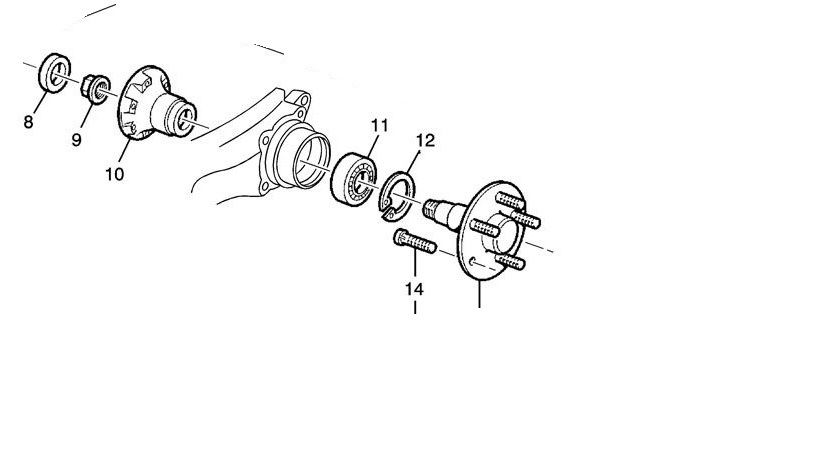