Greetings!
I am provided this calculation sheet for required wall thickness of finished cold bend but can't figure out from where the value 39.5 is taken and this calculation is for 8 inches Dia. why in row no. 58 its saying 12.70 wall thickness when we calculated wall thickness of pipe in above calculation in row 39 is 7.82 mm.
Kindly help me understand this.
Thanks
I am provided this calculation sheet for required wall thickness of finished cold bend but can't figure out from where the value 39.5 is taken and this calculation is for 8 inches Dia. why in row no. 58 its saying 12.70 wall thickness when we calculated wall thickness of pipe in above calculation in row 39 is 7.82 mm.
Kindly help me understand this.
Thanks
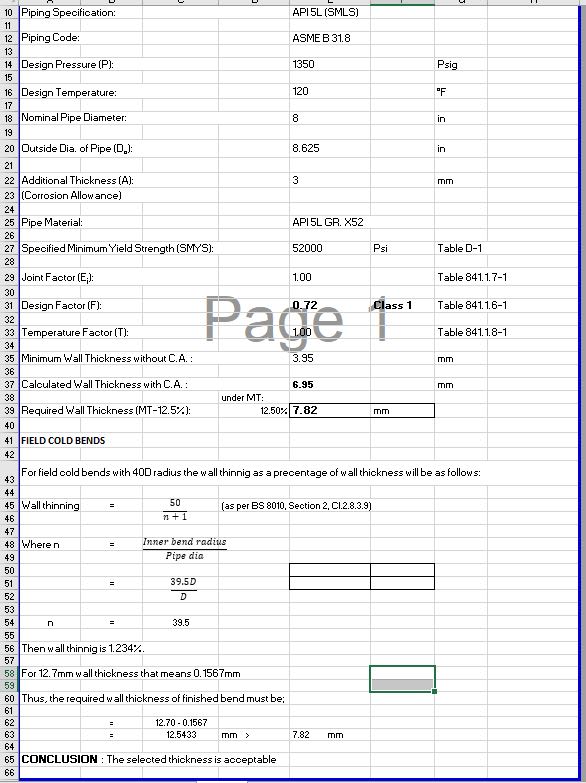