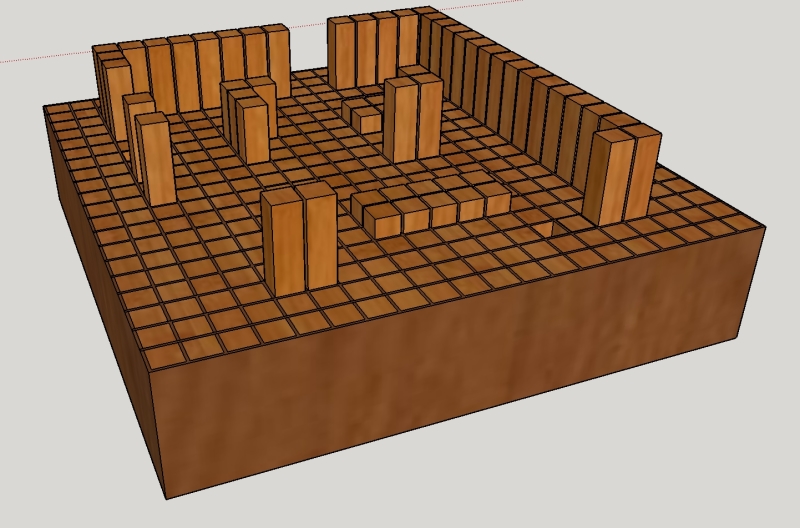
Hi Folks,
I'm pretty rusty when it comes to engineering and design having not worked directly in the area for awhile. I'm hoping someone may have some good suggestions for me. I'm trying to design a 20 x 20 matrix of columns which can be individually raised and lowered (only about 5" max) in any pattern desired. I'm at a loss to come up with an economical way to build something that allows individual movements of 400 columns. I've certainly considered linear actuators, but they are very expensive (especially x400). Would anyone have any suggestions? Thanks so much!
Scott