Hello,
We received a pump because it failed prematurely due to shaft breakage. After disassembly, we found that shaft was broken at throttle sleeve corner. Pump was last repaired about a year ago and shaft was not replaced. Can you tell what can be the failure reason? The pump ran for some years before this happened.
We received a pump because it failed prematurely due to shaft breakage. After disassembly, we found that shaft was broken at throttle sleeve corner. Pump was last repaired about a year ago and shaft was not replaced. Can you tell what can be the failure reason? The pump ran for some years before this happened.
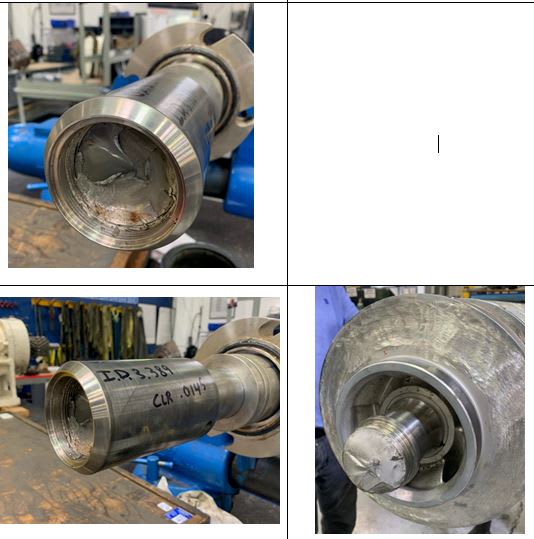