I have a new mat foundation that supports a tank and pump. For various reasons, the pump sits partially on our new foundation and partially on an existing foundation (grey). My concern is differential settlement that might induce some stresses on the pump piping. I've already explored other options (rotate pump 90 degrees, shift everything to right, etc.) and while some are possible, they have sizeable ramifications so I want to see if I can come up with a simple solution. My first idea is to have expansion joint material under the portion of the pump pad that sits on the existing foundation. In my mind, this would compress as the new foundation settles and should limit the differential. Thoughts? Other ideas?
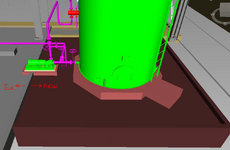
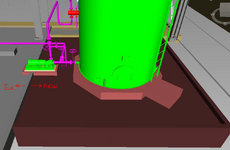