Sa-Ro
Mechanical
- Jul 15, 2019
- 279
Hi
Design requirements:
Datum B surface shall be perpendicular to datum A.
Hole shall be perp to datum B and located from datum A.
Length 50, 9 height, angular, radius shall be equally separated from hole axes.
Did I used correct GD&T?
Shall I use all around with datum B to control the 4 and 40
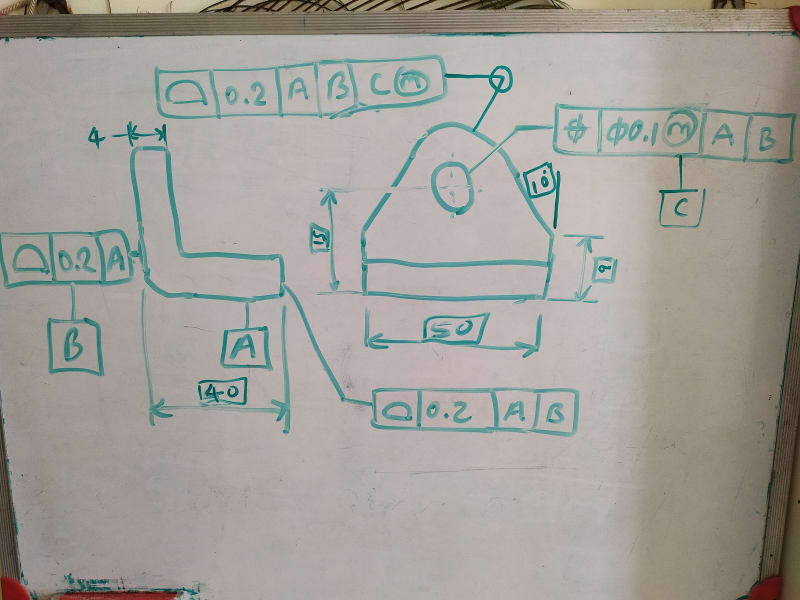
Design requirements:
Datum B surface shall be perpendicular to datum A.
Hole shall be perp to datum B and located from datum A.
Length 50, 9 height, angular, radius shall be equally separated from hole axes.
Did I used correct GD&T?
Shall I use all around with datum B to control the 4 and 40