We have a project that relating with pipeline system and pressure control, the project is actually having goal to knowing how much pressure drop will occurs in pipe line system that in initial condition the pressure inside the pipeline staying at steady or constant in particular psi and at the time in sudden, pressure will drop because of there are holes opened by a system that we have created before.
as you see above, that is probably the system or mechanism we created, so there is an obstacle (brown coloured) to blocking flow rate from upstream. The obstacle fixed by screws (red coloured) that will broken if there is a particular pressure of fluid in constant continously impacting the obstacle, we assume in 4000 PSI screws will be broken and in automatically the obstacle will goes forward and let the holes open and slowly flow rate of fluid pass through the holes and pressure of fluid will drop accordingly with area of those holes.
If
1. Diameter of hole : 20 mm
2. Diameter of pipe : 100 mm
3. Diameter of obstacle : 80 mm
4. P1 : 4000 PSI
how can we calculate the pressure drop ? which equation we have to use ? maybe someone may give us some advice, cause we have tried to calculate it with equation of bernoulli where (P1/rho + V1^2/2 = P2/rho + V2^2/2) but also we have a concern on about the volume changes due the obstacle, cause from the obstacle in first position where still fixed by screw and the obstacle after screw broken, is it also affecting 4000 PSI ? Cause there is volume changes from before and after screw broke ?
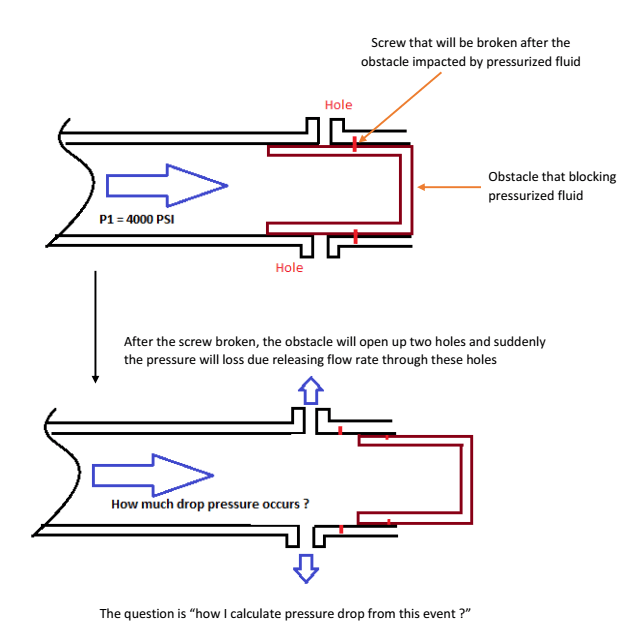
as you see above, that is probably the system or mechanism we created, so there is an obstacle (brown coloured) to blocking flow rate from upstream. The obstacle fixed by screws (red coloured) that will broken if there is a particular pressure of fluid in constant continously impacting the obstacle, we assume in 4000 PSI screws will be broken and in automatically the obstacle will goes forward and let the holes open and slowly flow rate of fluid pass through the holes and pressure of fluid will drop accordingly with area of those holes.
If
1. Diameter of hole : 20 mm
2. Diameter of pipe : 100 mm
3. Diameter of obstacle : 80 mm
4. P1 : 4000 PSI
how can we calculate the pressure drop ? which equation we have to use ? maybe someone may give us some advice, cause we have tried to calculate it with equation of bernoulli where (P1/rho + V1^2/2 = P2/rho + V2^2/2) but also we have a concern on about the volume changes due the obstacle, cause from the obstacle in first position where still fixed by screw and the obstacle after screw broken, is it also affecting 4000 PSI ? Cause there is volume changes from before and after screw broke ?