DoubleBoy
Mechanical
- Apr 19, 2018
- 2
Hi, I've got a high load pin supported by two bushing sleeves. It's picture below for illustration of this. I'm wondering how one would go about calculating bending in the sleeves by hand. The pin is routed all the way through the bushings through the next wall so it isn't like the entire load is applied to the end of the sleeve, but due to the pin deflecting I know the load wouldn't be applied at the wall either. Is there a good way to approximate the load amount and location or do I just have to rely on the FEA?
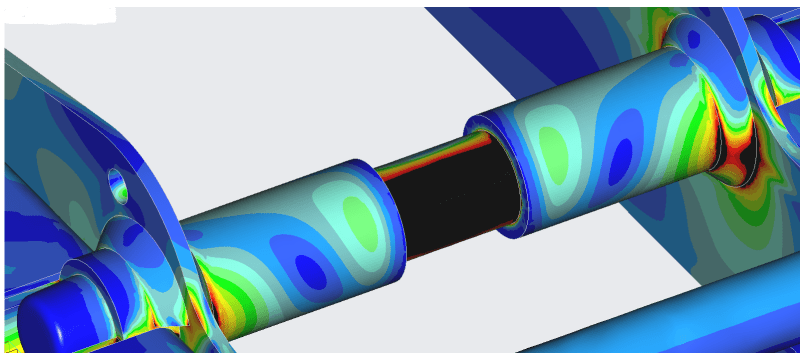