KootK
Structural
- Oct 16, 2001
- 18,590
I would like to produce some deflection vs uniform pressure diagrams for a 3mm thick aluminum panel product. I mistakenly thought that this would be easy and it's turned out to be rather difficult. I'm hoping that someone can either a) point me to a suitable method or b) confirm that no such method exists. Some thoughts/background:
- Per the graph below, non-linear membrane actions factor in significantly. I've erroneously used Timoshenko's small deflection equation to produce what is effectively my own version of the straight line. When I got to looking at the deflections, I realized that they greatly exceed the member thickness.
- Resource wise, I've got Timoshenko's plates and shells, Roarks, and most of the old papers cited in Roarks.
- While I don't need this to be super easy/simple, I don't want to get into FEM or Finite Difference with this. I also don't want to be assuming shape functions and doing virtual work in the form of variational calculus. This kind of thing is mentioned in the papers cited in Roarks. I'm sure that it's great stuff but I'm afraid that my math skills are not of a caliber that I'd trust myself to attempt this kind of a solution and pass it off to my client as results in which I was confident.
- Even if I can find a reasonable method to account for the membrane action, I suspect that most such solutions would assume the pinned supports to provide perfect in plane restraint to the panel edges. I doubt the truthiness of that in most applications. And assessing the surrounding structure for its contribution to membrane deformation would increase the scope of this assignment substantially. I know that, in many cases, panels can sort of create their own compression ring from which the membrane can be suspended. No doubt that's what happens with metal panel but, again, accounting for it simply seems to be a pretty tall order.
- I stumbled upon this document by Enclos. They actually propose a formula for this scenario but the equation got all jumbled on the greek variables. Anybody know what this equation is supposed to be?
I like to debate structural engineering theory -- a lot. If I challenge you on something, know that I'm doing so because I respect your opinion enough to either change it or adopt it.
- Per the graph below, non-linear membrane actions factor in significantly. I've erroneously used Timoshenko's small deflection equation to produce what is effectively my own version of the straight line. When I got to looking at the deflections, I realized that they greatly exceed the member thickness.
- Resource wise, I've got Timoshenko's plates and shells, Roarks, and most of the old papers cited in Roarks.
- While I don't need this to be super easy/simple, I don't want to get into FEM or Finite Difference with this. I also don't want to be assuming shape functions and doing virtual work in the form of variational calculus. This kind of thing is mentioned in the papers cited in Roarks. I'm sure that it's great stuff but I'm afraid that my math skills are not of a caliber that I'd trust myself to attempt this kind of a solution and pass it off to my client as results in which I was confident.
- Even if I can find a reasonable method to account for the membrane action, I suspect that most such solutions would assume the pinned supports to provide perfect in plane restraint to the panel edges. I doubt the truthiness of that in most applications. And assessing the surrounding structure for its contribution to membrane deformation would increase the scope of this assignment substantially. I know that, in many cases, panels can sort of create their own compression ring from which the membrane can be suspended. No doubt that's what happens with metal panel but, again, accounting for it simply seems to be a pretty tall order.
- I stumbled upon this document by Enclos. They actually propose a formula for this scenario but the equation got all jumbled on the greek variables. Anybody know what this equation is supposed to be?
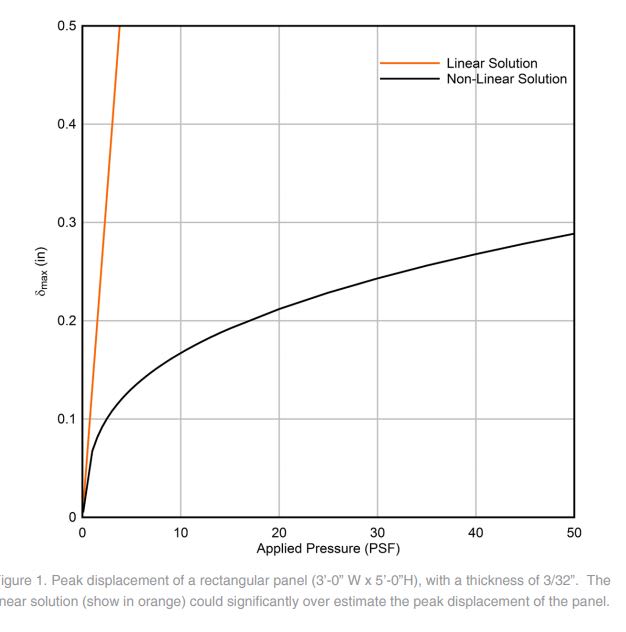
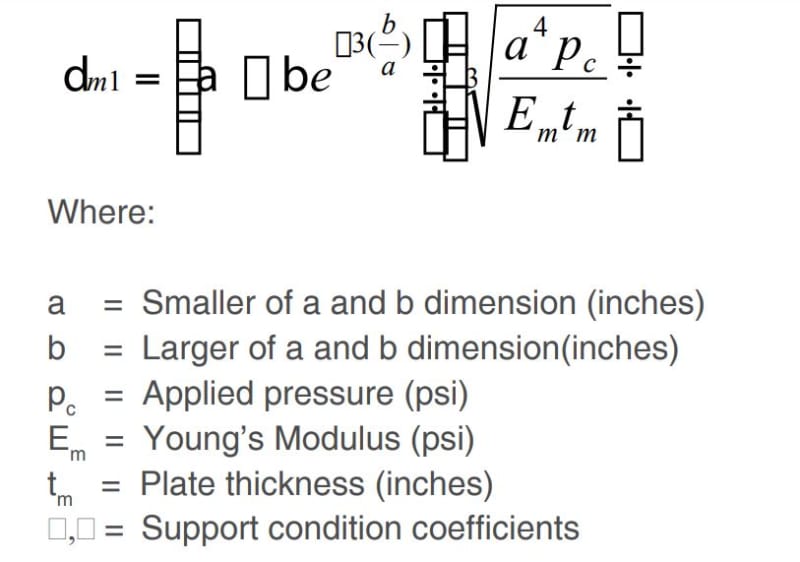
I like to debate structural engineering theory -- a lot. If I challenge you on something, know that I'm doing so because I respect your opinion enough to either change it or adopt it.