Deven_Patel
Mechanical
Hello,
I'm working on an astronomical study project that entails building a mount for a telescope. I'm working on the mechanical aspect and I am designing the mount at the moment, but I've run into some questions about how I should go about designing the joints for the mounts (1&2 in the picture) and the platform (3 in the picture) that the mounts will be fixed to. I was thinking about designing flanges at the base of the mounts to fix them to the platform in a precise and secure manner. Reducing the propagation of mechanical vibrations that the platform may be subjected to is also a concern. Any thoughts about the flange idea? Or recommendations for another method?
Thanks in advance guys!
Deven Patel
I'm working on an astronomical study project that entails building a mount for a telescope. I'm working on the mechanical aspect and I am designing the mount at the moment, but I've run into some questions about how I should go about designing the joints for the mounts (1&2 in the picture) and the platform (3 in the picture) that the mounts will be fixed to. I was thinking about designing flanges at the base of the mounts to fix them to the platform in a precise and secure manner. Reducing the propagation of mechanical vibrations that the platform may be subjected to is also a concern. Any thoughts about the flange idea? Or recommendations for another method?
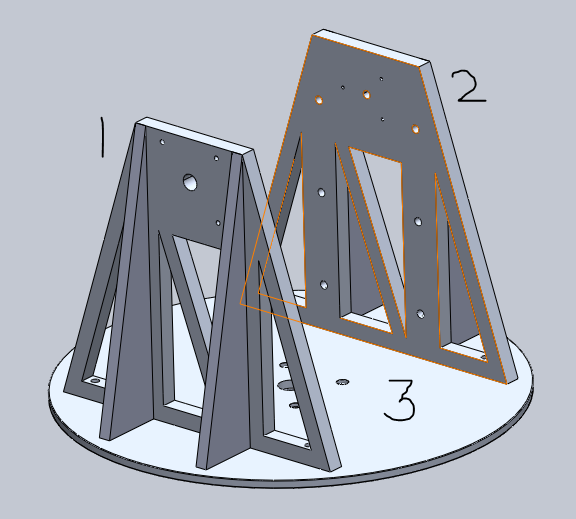
Thanks in advance guys!
Deven Patel