TugboatEng
Marine/Ocean
Today I have inherited several vessels with obsolete drive units and no factory support. The drives have submerged.structural flanges and are notorious for breaking bolts. 30 years later, I think it's time to look into a cause. The fastener are socket head caps screws of ASTM A574 standard and some shoulder bolts of no specific standard. My understanding is that the shoulder bolts have never been found broken. It appears the shoulder bolts are 7/8" and 32 HRC. The bolts that are breaking are 1-1/8" and 37 HRC. Another manufacturer of similar equipment uses exclusively class 8.8 fasteners, I assume to reduce the risk of hydrogen embrittlement.
Here is a picture of one failed fastener. Are their any visual clues of HE? Can HE be determined if the fracture faces are corroded?
I'm thinking of specifying ASTM A193 B7. The problem is that lower strength socket head cap screws are not commercially available in imperial dimensions.
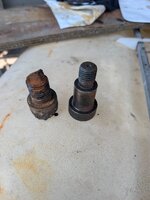
Here is a picture of one failed fastener. Are their any visual clues of HE? Can HE be determined if the fracture faces are corroded?
I'm thinking of specifying ASTM A193 B7. The problem is that lower strength socket head cap screws are not commercially available in imperial dimensions.
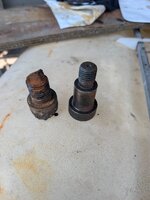