RFreund
Structural
- Aug 14, 2010
- 1,885
The steel fabricator would like to use an end plate moment connection for connecting an HSS to a WF column. Not sure how I feel about it. I suppose I can try to follow the DG4, but only having exterior bolts "feels odd".
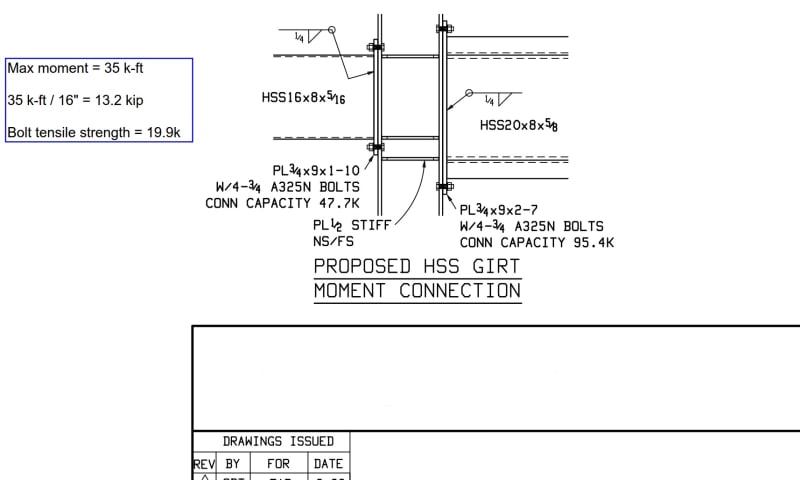