goodblasson
Mechanical
Hello Guys, this is my first post so go easy on me. I am working on a project at work, I have to design a motorized cart that can move up to a 5,000lb load. The cart is 72" long, 27" wide, and 30" tall, it has arms that hold rollers which a 8" diameter tool sits on the rollers. The cart has to move up to 3mph and the 4 wheels are 8" diameter and made of steel and roll on inverted angle iron(like a train track). Anyhow, the customer wants to see a DC motor used and have the power supply onboard. It has to have some kind of control to start slow and gain speed up to 3mph and slow down to stop. My problem is that I can not find a DC motor and gear setup to propel the cart at 3mph and handle the load. Can anyone give me any input or suggestions please? I was thinking of buying a motorized pallet jack and modify it so that I can connect it to my cart for propulsion. But obviously thats the cheap and ugly way out of my problem. I am including a picture of a cart another customer uses, but they will not give me any details to the build so I am on my own....
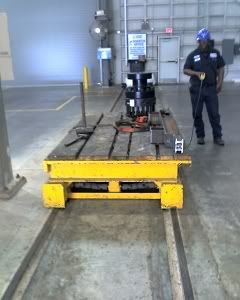
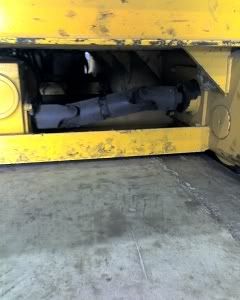
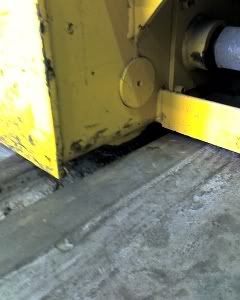