IBRCAN
Electrical
- Feb 3, 2012
- 53
Hello All,
I am a technician working for a dealer selling one of the leading generator brands. I've been tasked with performing a failure analysis on a unit that was overhauled and experienced a major failure shortly after start up. I know there are some folks on this forum who are very experienced with generators. I'm still at the fact gathering stage, and starting to form some theories regarding root cause. Here are some facts:
-V12 680 kw (prime), 600V, 60Hz, 1800 RPM diesel generator set
-Generator end is random wound, 4 pole, single bearing
-Came into shop for major overhaul based on hours (no failure)
-Engine was complete overhauled in house by a very experienced diesel mechanic. Engine endplay prior to attaching generator was within spec.
-Generator end (alternator) was send to a local motor shop for cleaning, re-insulating, and re-bearing
-During unloading of alternator back at our shop, the alternator was accidentally dropped, and therefore sent back to said motor shop for inspection
-I will call the motor shop to find out exactly what was done to repair, but I see weld marks on the rear bearing housing and apparently the rotor shaft was bent.
-Rebuilt engine and alternator were assembled. I spoke with the tech who performed the assembly and unfortunately engine end-play was NOT checked after assembly.
-Went to load test the rebuild unit and within 15 minutes after start up a major failure was observed--the rear crankshaft thrust plate has been ground down and it is obvious the block got very hot due to the amount of force applied axially to the crankshaft, apparently by the generator end. The forward crankshaft thrust plate is like new.
-End-play was checked prior to disassembly--no end-play was measured.
It is APPARENT that the motor shop did something which caused a change. This generator end had been mated to this engine for 30,000 hours previously with no issues. Either the rotor shaft effective length is LONGER due to incorrect assembly or machining, OR my other thought is that magnetic centre of the alternator somehow changed. I believe they had to strip the rotor shaft in order to repair it--perhaps the rotor was re-wound off say 1/4" if that is possible. I understand the concept of magnetic centre, but don't know how I would go about confirming/dismissing it as a potential cause. It is my understand that a motor/generator rotor can exert several hundred pounds of force in trying to run in magnetic centre.
Anyway, just looking to get a discussion going--I'll post more information as I obtain it.
Regards
Ian
FYI, pic is of #4 main bearing journal, front thrust washer still intact, and what remains of the rear thrust washer.
I am a technician working for a dealer selling one of the leading generator brands. I've been tasked with performing a failure analysis on a unit that was overhauled and experienced a major failure shortly after start up. I know there are some folks on this forum who are very experienced with generators. I'm still at the fact gathering stage, and starting to form some theories regarding root cause. Here are some facts:
-V12 680 kw (prime), 600V, 60Hz, 1800 RPM diesel generator set
-Generator end is random wound, 4 pole, single bearing
-Came into shop for major overhaul based on hours (no failure)
-Engine was complete overhauled in house by a very experienced diesel mechanic. Engine endplay prior to attaching generator was within spec.
-Generator end (alternator) was send to a local motor shop for cleaning, re-insulating, and re-bearing
-During unloading of alternator back at our shop, the alternator was accidentally dropped, and therefore sent back to said motor shop for inspection
-I will call the motor shop to find out exactly what was done to repair, but I see weld marks on the rear bearing housing and apparently the rotor shaft was bent.
-Rebuilt engine and alternator were assembled. I spoke with the tech who performed the assembly and unfortunately engine end-play was NOT checked after assembly.
-Went to load test the rebuild unit and within 15 minutes after start up a major failure was observed--the rear crankshaft thrust plate has been ground down and it is obvious the block got very hot due to the amount of force applied axially to the crankshaft, apparently by the generator end. The forward crankshaft thrust plate is like new.
-End-play was checked prior to disassembly--no end-play was measured.
It is APPARENT that the motor shop did something which caused a change. This generator end had been mated to this engine for 30,000 hours previously with no issues. Either the rotor shaft effective length is LONGER due to incorrect assembly or machining, OR my other thought is that magnetic centre of the alternator somehow changed. I believe they had to strip the rotor shaft in order to repair it--perhaps the rotor was re-wound off say 1/4" if that is possible. I understand the concept of magnetic centre, but don't know how I would go about confirming/dismissing it as a potential cause. It is my understand that a motor/generator rotor can exert several hundred pounds of force in trying to run in magnetic centre.
Anyway, just looking to get a discussion going--I'll post more information as I obtain it.
Regards
Ian
FYI, pic is of #4 main bearing journal, front thrust washer still intact, and what remains of the rear thrust washer.
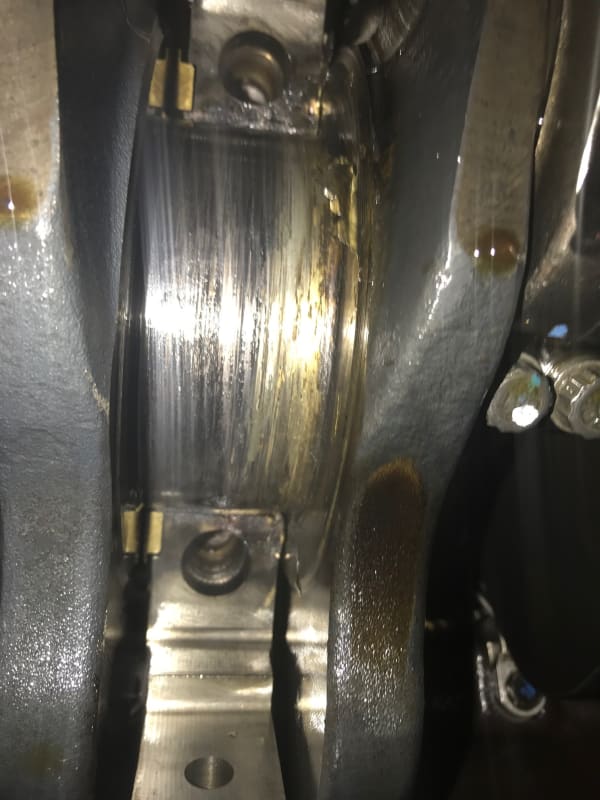