I'm evaluating the capacity of the split vertical mullion system shown below. For the evaluation of flange local buckling, I'm treating the blue and red flanges as though neither braces the other in any way. And that's resulting in very low capacities. Much lower, in fact, that the span charts of other manufacturers would indicate for similar products (Kawneer, Toro, etc).
So my question is this: could I rationally justify either the blue or red flange being braced against local compression buckling at their tips? Or could the red flange be considered to only cantilever from its "connection" to the blue flange? Treating the flanges this way, instead of as fully cantilevered from the side walls, makes a large difference with respect to capacity.
In the wild, I fully expect that this flange buckling would see some kind of restraint. Justifying that to be relied upon for a design assumption is another matter altogether however. There will eventually be some testing.
I like to debate structural engineering theory -- a lot. If I challenge you on something, know that I'm doing so because I respect your opinion enough to either change it or adopt it.
So my question is this: could I rationally justify either the blue or red flange being braced against local compression buckling at their tips? Or could the red flange be considered to only cantilever from its "connection" to the blue flange? Treating the flanges this way, instead of as fully cantilevered from the side walls, makes a large difference with respect to capacity.
In the wild, I fully expect that this flange buckling would see some kind of restraint. Justifying that to be relied upon for a design assumption is another matter altogether however. There will eventually be some testing.
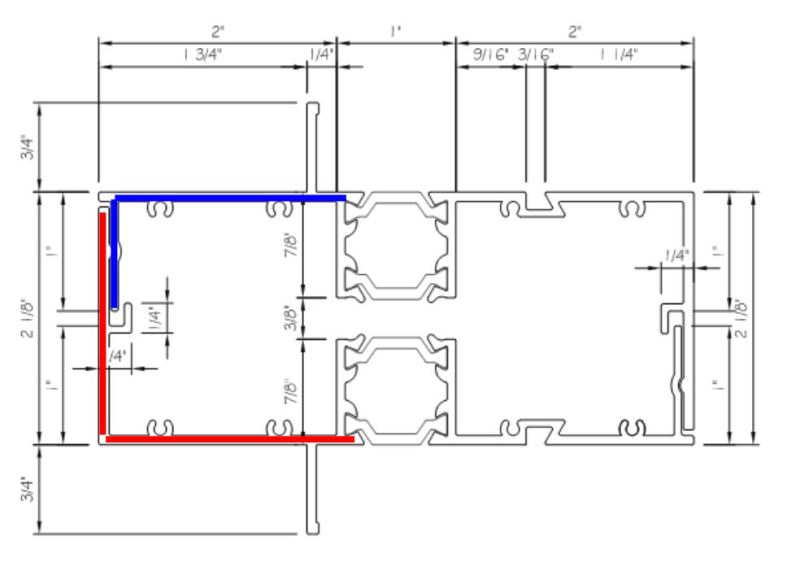
I like to debate structural engineering theory -- a lot. If I challenge you on something, know that I'm doing so because I respect your opinion enough to either change it or adopt it.