LeonhardEuler
Structural
Hello,
I am trying to analyze a FEMAP model with somewhat uniqe geometry. When I make my model in my modeling program I make an object as all one solid, but when I bring the .stp file into FEMAP it makes the object into 50 solids, or so. Why is this and how can I avoid this so the analysis is more manageable? I am getting many connection errors trying to connect all of these solids with auto connect?
Also I have a cylindrical object in this assembly and meshing it has proved to be near impossible for some reason with the mesh solid command and the default mesh sizes.
Thanks for any help. link to model
p.s. can anyone give me a reference to learn how to make a contact simulation when objects aren't touching at first, but will be after force is applied.
I am trying to analyze a FEMAP model with somewhat uniqe geometry. When I make my model in my modeling program I make an object as all one solid, but when I bring the .stp file into FEMAP it makes the object into 50 solids, or so. Why is this and how can I avoid this so the analysis is more manageable? I am getting many connection errors trying to connect all of these solids with auto connect?
Also I have a cylindrical object in this assembly and meshing it has proved to be near impossible for some reason with the mesh solid command and the default mesh sizes.
Thanks for any help. link to model
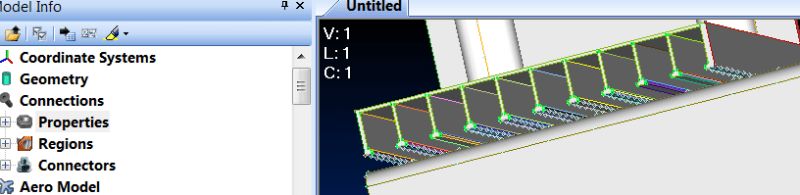
p.s. can anyone give me a reference to learn how to make a contact simulation when objects aren't touching at first, but will be after force is applied.
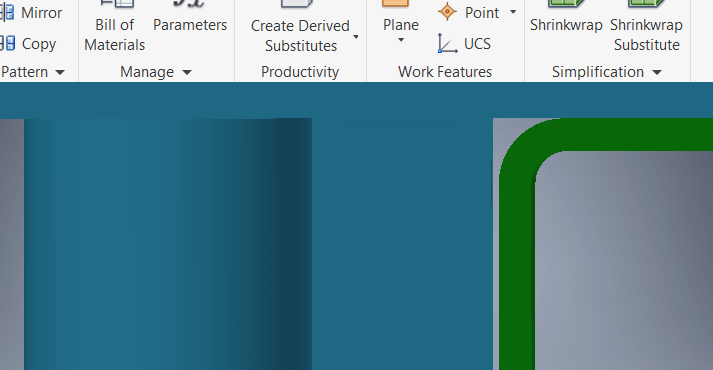