All,
Thermodynamics was a lifetime ago and I have never needed it for my day to day. Until now, that is. I have been handed an application that has a significant thermal component. We are lifting a vessel that will be at temperature, as high as 350C. Our tooling will grab around (but not squeeze) the neck of the vessel. It's somewhat similar to the picture I've included of a barrel lifting attachment. There is a lip at the top of the vessel that will be used for the lifting purposes, i.e. we will not be lifting via friction forces from a gripping type of action. Somewhat like the hanging wine glass rack that I've also included. We need to run an FEA analysis of our design. Normally this is something we do every day, but the thermal load puts it into a whole new category. For reference, we are using Solidworks Simulation 2024. When I run a static study on the tooling without thermal I get a max stress of 19.4 ksi. I created a second study that includes 350C on the face that will contact the lip of the vessel. The max stress jumps to 174 ksi (9 times increase). However, the high stress zone does not appear to extend very deep into the material.
What I don't know is how to interpret these results with the thermal (or even know if my approach is correct for that matter). I am hoping that someone with a lot more thermal experience than I can offer some guidance. At what point do you have to worry about thermal cracking, fatigue, creep, etc.? What do the stress results of the high temp contact area really mean? Of course, there is material selection, insulating coatings, and the like, but I am just trying to get my feet off the ground at the moment. I'll make the leap to Inconel later.
I appreciate any insight that you can offer. Unfortunately, due to the nature of this project I cannot share any specific details of what we're working on, but I think the two examples I gave are reasonably close analogs for what's going on..
Thanks in advance,,
Aaron
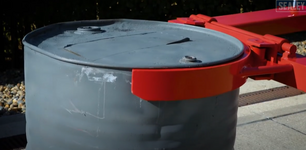
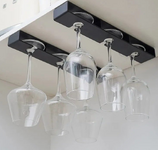
Thermodynamics was a lifetime ago and I have never needed it for my day to day. Until now, that is. I have been handed an application that has a significant thermal component. We are lifting a vessel that will be at temperature, as high as 350C. Our tooling will grab around (but not squeeze) the neck of the vessel. It's somewhat similar to the picture I've included of a barrel lifting attachment. There is a lip at the top of the vessel that will be used for the lifting purposes, i.e. we will not be lifting via friction forces from a gripping type of action. Somewhat like the hanging wine glass rack that I've also included. We need to run an FEA analysis of our design. Normally this is something we do every day, but the thermal load puts it into a whole new category. For reference, we are using Solidworks Simulation 2024. When I run a static study on the tooling without thermal I get a max stress of 19.4 ksi. I created a second study that includes 350C on the face that will contact the lip of the vessel. The max stress jumps to 174 ksi (9 times increase). However, the high stress zone does not appear to extend very deep into the material.
What I don't know is how to interpret these results with the thermal (or even know if my approach is correct for that matter). I am hoping that someone with a lot more thermal experience than I can offer some guidance. At what point do you have to worry about thermal cracking, fatigue, creep, etc.? What do the stress results of the high temp contact area really mean? Of course, there is material selection, insulating coatings, and the like, but I am just trying to get my feet off the ground at the moment. I'll make the leap to Inconel later.
I appreciate any insight that you can offer. Unfortunately, due to the nature of this project I cannot share any specific details of what we're working on, but I think the two examples I gave are reasonably close analogs for what's going on..
Thanks in advance,,
Aaron
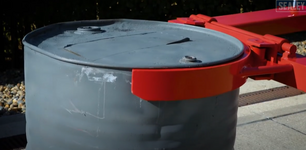
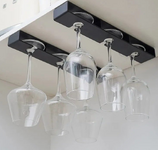