SabrinaPAE
Civil/Environmental
Hi all,
I'm new to this forum, but am struggling with an error message I am receiving in EPANET.
I am modeling the existing water system for a University in West Michigan. I am using a tank as the supply to the system, and adding nodes to respective locations to add demand to buildings in the University.
There are two double check valves/back flow preventers at the beginning of the system that I am modeling as a GPV with a head loss curve. There are three hydrant flow tests I am using to calibrate my system. When I place no demand on any hydrant and run the model, I get an error message saying that the system is unbalanced at 0+00 hours. However, when I place demand on any one hydrant, the model runs fine...
I can not figure out why this is happening for the life of me, and would really appreciate some input. I've attached the .net file for the system I am modeling.
If anyone has any tips, I would be extremely grateful!
Thanks!
See below for a .jpeg snapshot of the system:
I'm new to this forum, but am struggling with an error message I am receiving in EPANET.
I am modeling the existing water system for a University in West Michigan. I am using a tank as the supply to the system, and adding nodes to respective locations to add demand to buildings in the University.
There are two double check valves/back flow preventers at the beginning of the system that I am modeling as a GPV with a head loss curve. There are three hydrant flow tests I am using to calibrate my system. When I place no demand on any hydrant and run the model, I get an error message saying that the system is unbalanced at 0+00 hours. However, when I place demand on any one hydrant, the model runs fine...
I can not figure out why this is happening for the life of me, and would really appreciate some input. I've attached the .net file for the system I am modeling.
If anyone has any tips, I would be extremely grateful!
Thanks!
See below for a .jpeg snapshot of the system:
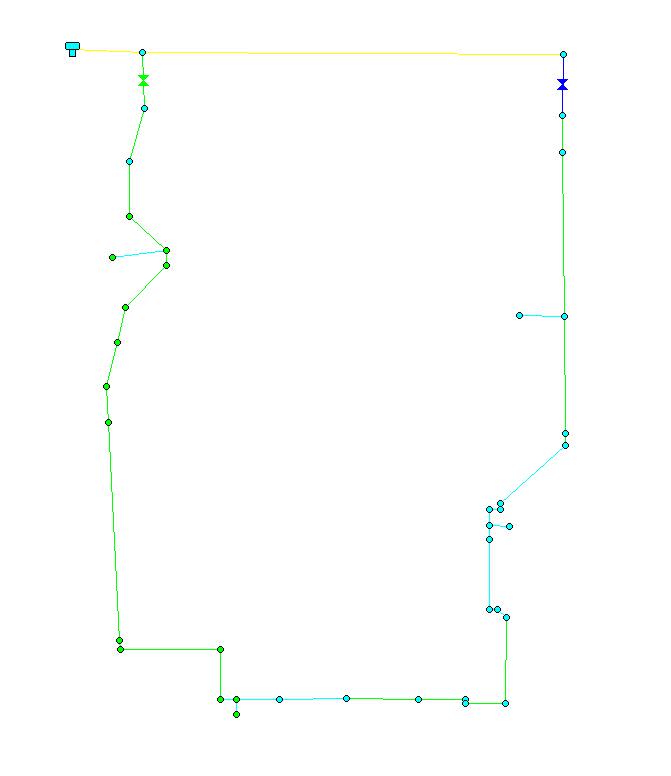