efFeb
Structural
- Dec 25, 2019
- 68
Good Afternoon,
I am designing a steel transfer structure which includes box girders. I have a couple of instances where the box girder depth must reduce at a step. I plan to include a stiff plate at this transition, but want to be sure that I have all of my bases covered for the plate bending stresses to be considered here. The beam is in positive bending at the location of the step, and I am thinking about the following:
1. Bending of the plate above the reduced-depth section -- this is difficult for me to really visualize happening, as the two webs would have to bend in plane over the flange of the lower section
2. bending of the plate between the two webs of the full-depth section -- it is difficult for me to imagine this stress being very large; the distance between webs is short and the plate is not stiff relative to the sections themselves.
I've attached an image below to show these conditions I am thinking of:
Because I am not convinced that either of these conditions could result in significant plate bending, I am wondering if there are additional forces that I am not considering yet.
If anyone has any input or resources that relate to this condition, that would be fantastic.
Thank-you so much!
I am designing a steel transfer structure which includes box girders. I have a couple of instances where the box girder depth must reduce at a step. I plan to include a stiff plate at this transition, but want to be sure that I have all of my bases covered for the plate bending stresses to be considered here. The beam is in positive bending at the location of the step, and I am thinking about the following:
1. Bending of the plate above the reduced-depth section -- this is difficult for me to really visualize happening, as the two webs would have to bend in plane over the flange of the lower section
2. bending of the plate between the two webs of the full-depth section -- it is difficult for me to imagine this stress being very large; the distance between webs is short and the plate is not stiff relative to the sections themselves.
I've attached an image below to show these conditions I am thinking of:
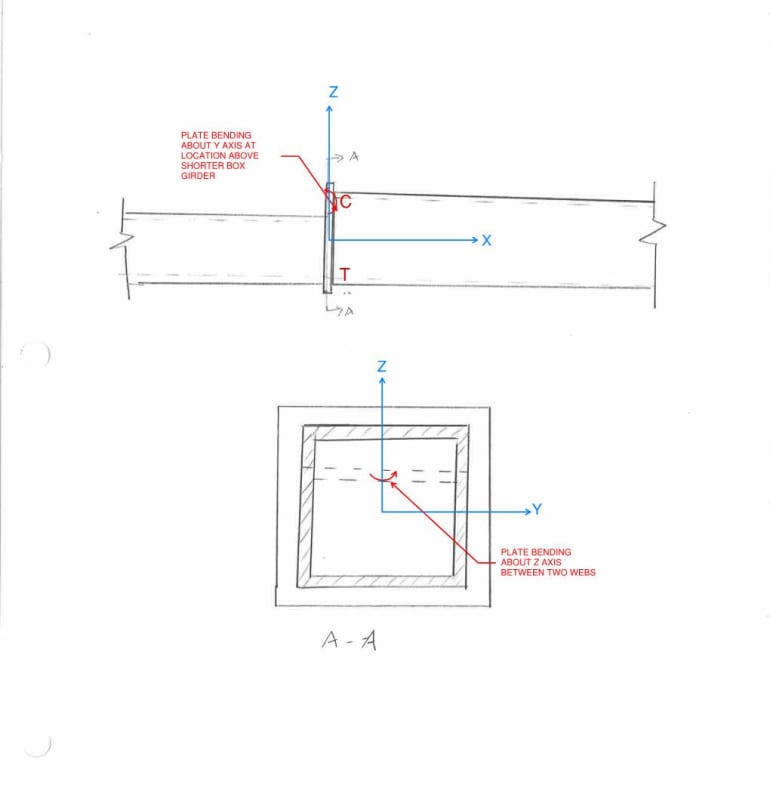
Because I am not convinced that either of these conditions could result in significant plate bending, I am wondering if there are additional forces that I am not considering yet.
If anyone has any input or resources that relate to this condition, that would be fantastic.
Thank-you so much!