Hi
Does anyone a good design approach to the detailed design of a burst/rupture disk connections. As below this is the connection of a short stub to the mainline. The thrust force from the disk puts a large force trough the stub to main connection and around the pipe shoe under the connection.
We have checked the stress with FEA (Nozzpro) and find high stress at the edge of the stub weld. The stub has to be very thick before this stress is under code.
Is there a better detail?
We have seen reinforcing rings welded from the stub around to the pipe shoe.
Thanks.
Does anyone a good design approach to the detailed design of a burst/rupture disk connections. As below this is the connection of a short stub to the mainline. The thrust force from the disk puts a large force trough the stub to main connection and around the pipe shoe under the connection.
We have checked the stress with FEA (Nozzpro) and find high stress at the edge of the stub weld. The stub has to be very thick before this stress is under code.
Is there a better detail?
We have seen reinforcing rings welded from the stub around to the pipe shoe.
Thanks.
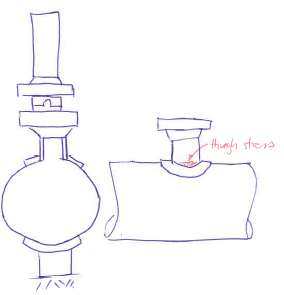