tugni925
Mechanical
- Sep 14, 2020
- 107
The cube on top is supposed to be made of concrete, which due to the hardening there will be thermal expansion, and residual stress occur. This will create normal pressure between the plate and cube if I understand it correctly. I am new to this, and I was wondering if someone could explain to me what is happening in this model.
Predefined field settings, this is the one I have biggest trouble understanding. How does the different options affect the model? (Direct specification, constant through region and "1"):
Material properties for the concrete cube:
The first three boundary conditions lock translation in U1, U2 and U3 respectively. Why did they not just pin the entire plate in one BC's instead of doing it in three different BC's.
Cube translation in U3 is restricted so it cannot expand upwardsw. I assume this is to cause normal pressure at the bottom as it will have to expand towards the plate.
Reference point is made, kinematic coupling to the face of the cube, and the cube is pushed 1 in the first direction. This is to simulate sliding.
Predefined field settings, this is the one I have biggest trouble understanding. How does the different options affect the model? (Direct specification, constant through region and "1"):
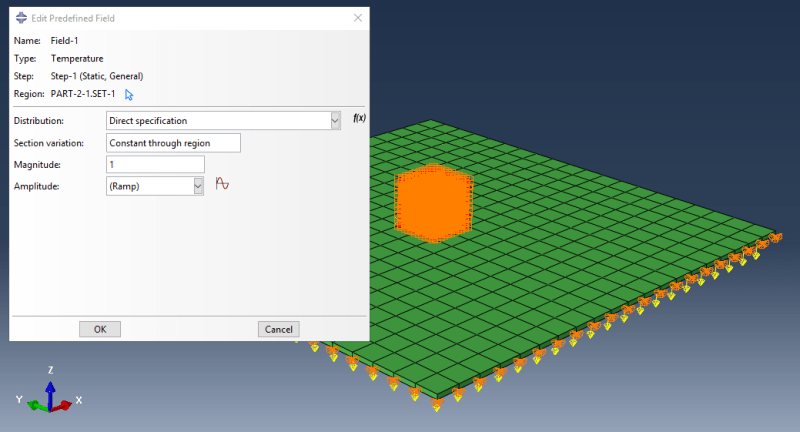
Material properties for the concrete cube:
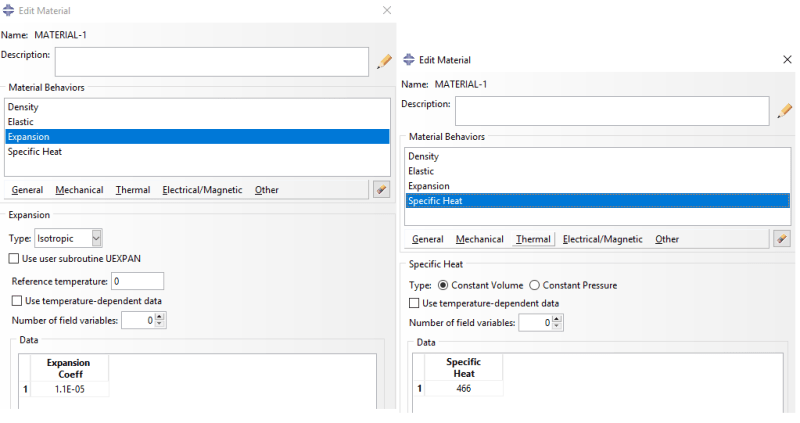
The first three boundary conditions lock translation in U1, U2 and U3 respectively. Why did they not just pin the entire plate in one BC's instead of doing it in three different BC's.
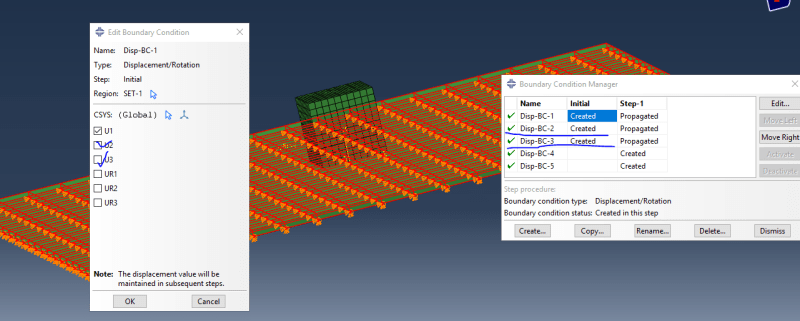
Cube translation in U3 is restricted so it cannot expand upwardsw. I assume this is to cause normal pressure at the bottom as it will have to expand towards the plate.
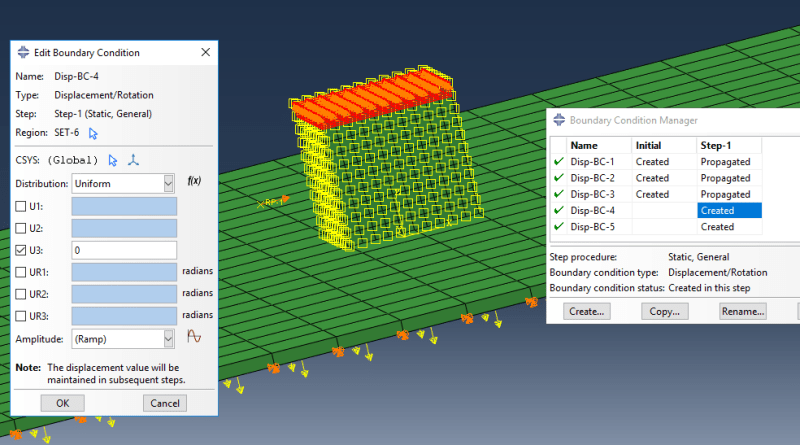
Reference point is made, kinematic coupling to the face of the cube, and the cube is pushed 1 in the first direction. This is to simulate sliding.
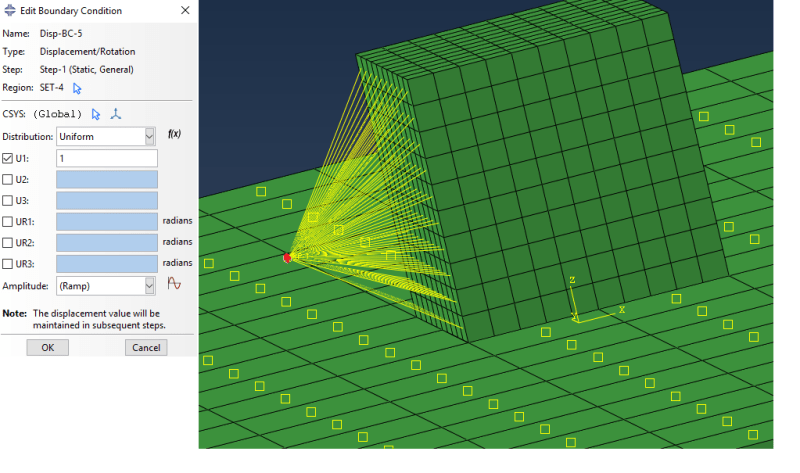