martinrelayer
Electrical
Hello,
In a wastewater plant, there´s installed HDG cable trays with what seemed good HDG bolts (same supplier)
No some years passed and only see the bolts rusted.
What could cause this in particular and what can be done?
Replacing bolts from same material Hot dip galvanized seem to have the same future as now.
This rustiness is only three yeear operation.
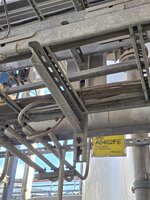
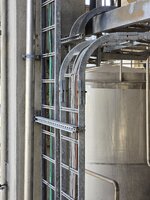
In this other picture is the bonding for the frame of the machine, this is tin plated copper terminal and copper cable over stainless steel. What do you recommend to make the bonding to this material in such environment? you can see terminal looks totally rusted.
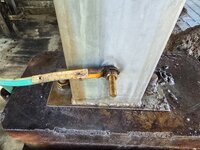
Thanks in advance,
Martin.
In a wastewater plant, there´s installed HDG cable trays with what seemed good HDG bolts (same supplier)
No some years passed and only see the bolts rusted.
What could cause this in particular and what can be done?
Replacing bolts from same material Hot dip galvanized seem to have the same future as now.
This rustiness is only three yeear operation.
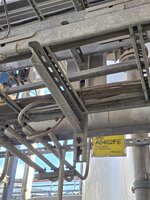
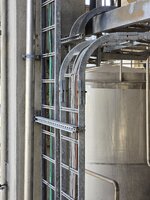
In this other picture is the bonding for the frame of the machine, this is tin plated copper terminal and copper cable over stainless steel. What do you recommend to make the bonding to this material in such environment? you can see terminal looks totally rusted.
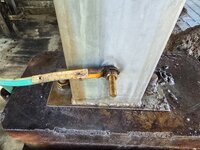
Thanks in advance,
Martin.