greznik91
Structural
- Feb 14, 2017
- 186
Hi, I have a question about connecting timber roof beams.
Since its pretty common, that roof beam consists from more than 1 element (span of several meters) we have to connect its elements.
So if we have 3 elements we can connect them at/above supports (walls/columns)- MODEL 3 in picture. Other option is to make a connection at a point where bending moment diagram is zero - MODEL 2 in picture.
I found out that in MODEL 3 there are always bigger deflections which often causes problems and demands bigger beams. MODEL 2 has much lesser deflections at same load and geometry...
But what Im wondering about is what do we do about shear forces that acts AT connection (node) in MODEL 2?
How do we control it on shear force? in picture we have a shear force of 25 kN there...Element is 20/24 cm, timber C24.
I have never seen any project where engineer made a control of connection like this for a shear force. Why is that?
Since its pretty common, that roof beam consists from more than 1 element (span of several meters) we have to connect its elements.
So if we have 3 elements we can connect them at/above supports (walls/columns)- MODEL 3 in picture. Other option is to make a connection at a point where bending moment diagram is zero - MODEL 2 in picture.
I found out that in MODEL 3 there are always bigger deflections which often causes problems and demands bigger beams. MODEL 2 has much lesser deflections at same load and geometry...
But what Im wondering about is what do we do about shear forces that acts AT connection (node) in MODEL 2?
How do we control it on shear force? in picture we have a shear force of 25 kN there...Element is 20/24 cm, timber C24.
I have never seen any project where engineer made a control of connection like this for a shear force. Why is that?
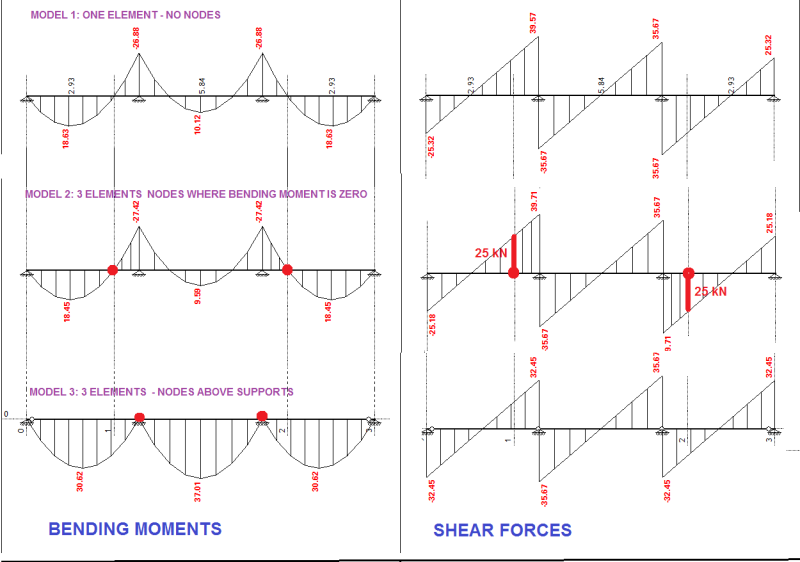
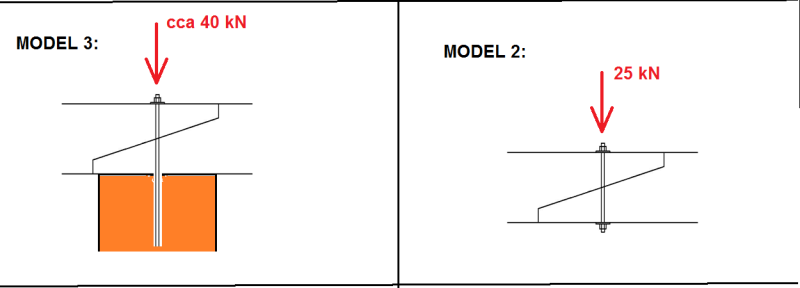