KootK
Structural
- Oct 16, 2001
- 18,590
I've got a CFM truss supported (not cantilevered) from a CFM wall system. What's the best way to do this? Thoughts:
- I suppose one could do an LVL ledger.
- One could also do a light gauge ledger but that would require stiffening at each truss, right?
- I'd like to mess with the envelope as little as possible.
- Would like to tie the roof diaphragm into the wall diaphragm at least nominally.
- Sometimes I'll likely be hitting CFM headers instead of wall studs.
- This may not work so hot when a truss lands right on a walls stud.
I find CFM trusses to be a pain in that, until a supplier is chosen, I won't actually know what the chords etc will look like. With wood trusses, they make a big deal of truss-to-building connections being by the EOR. Here, it's tough to comply with that. Hard to know just how to connect something when you don't quite know what that something is. There's quite a variety in possible chord profiles.
I like to debate structural engineering theory -- a lot. If I challenge you on something, know that I'm doing so because I respect your opinion enough to either change it or adopt it.
- I suppose one could do an LVL ledger.
- One could also do a light gauge ledger but that would require stiffening at each truss, right?
- I'd like to mess with the envelope as little as possible.
- Would like to tie the roof diaphragm into the wall diaphragm at least nominally.
- Sometimes I'll likely be hitting CFM headers instead of wall studs.
- This may not work so hot when a truss lands right on a walls stud.
I find CFM trusses to be a pain in that, until a supplier is chosen, I won't actually know what the chords etc will look like. With wood trusses, they make a big deal of truss-to-building connections being by the EOR. Here, it's tough to comply with that. Hard to know just how to connect something when you don't quite know what that something is. There's quite a variety in possible chord profiles.
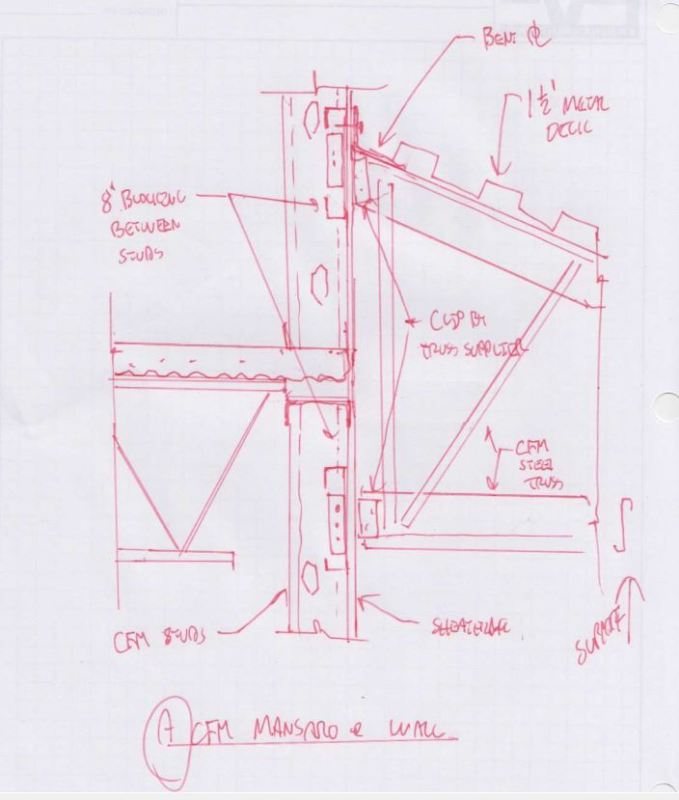
I like to debate structural engineering theory -- a lot. If I challenge you on something, know that I'm doing so because I respect your opinion enough to either change it or adopt it.