AaronMcD
Structural
- Aug 20, 2010
- 273
We are designing a display structure made up of HSS4x4x1/4 tubes that will require field assembly of all parts. It is a space frame, and deflection/vibration is the primary concern.
We are looking into bolted connections. The final dimension of beams and posts will be 6"x6" so we can't have bolts sticking out far.
This is the only thing I can think of, using slip critical bolts and a slotted connection. Among my concerns:
1) The slot at the end will cause some slight benting of individual HSS quarters due to eccentric shear. However, the slip critical connection - washer plates and internal plates likely provide enough stiffness and shear transfer.
2) Long individual plates will have angular deformation from the weld process. This is why I specify to leave in the erection bolt, which in turn is why I need slotted holes. I am worried that if try and compensate for angular deformation the plates may be too far off for proper connection in the field.
3) Are the welded nuts allowed, and will they provide enough torsion resistance during bolt tensioning?
4) I have already checked to be sure the first bolt will bring the plates into contact under a very small portion of it's total load. I will probably have to ensure that the bolt nearest the connection in tensioned first.
5) It's really weird and might scare whoever has to install it lol
We are looking into bolted connections. The final dimension of beams and posts will be 6"x6" so we can't have bolts sticking out far.
This is the only thing I can think of, using slip critical bolts and a slotted connection. Among my concerns:
1) The slot at the end will cause some slight benting of individual HSS quarters due to eccentric shear. However, the slip critical connection - washer plates and internal plates likely provide enough stiffness and shear transfer.
2) Long individual plates will have angular deformation from the weld process. This is why I specify to leave in the erection bolt, which in turn is why I need slotted holes. I am worried that if try and compensate for angular deformation the plates may be too far off for proper connection in the field.
3) Are the welded nuts allowed, and will they provide enough torsion resistance during bolt tensioning?
4) I have already checked to be sure the first bolt will bring the plates into contact under a very small portion of it's total load. I will probably have to ensure that the bolt nearest the connection in tensioned first.
5) It's really weird and might scare whoever has to install it lol
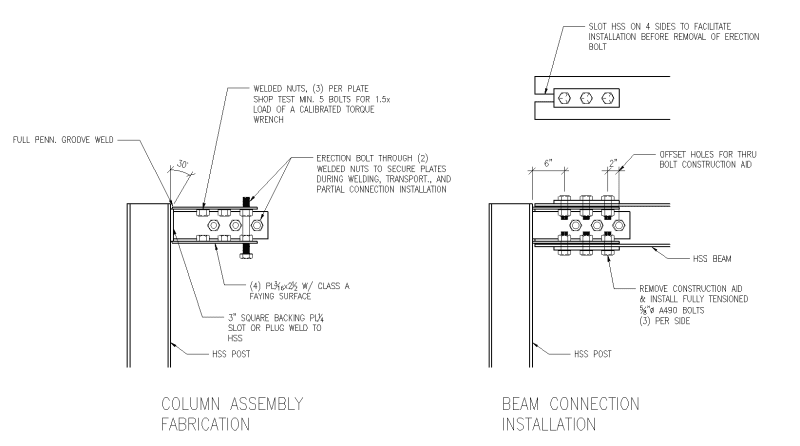