I know this question has been asked a few times. I'm sure I checked almost every answer avaiable around. But I'm still having trouble using SOL 105 buckling with inertial relief.
Here's the .nas/.dat Nastran file: https://drive.google.com/file/d/1RrH_hMMeLpE3qEWH_Ea3nuVQBoBBindj/view?usp=drivesdk
Here's the error I'm having in the buckling set, from the f06 file:

I have INREL set to -1 in the Bulk Data:
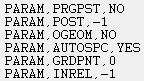
I also have SUPORT1 defined in the Bulk Data:

And finally I'm running a STATIC SUBCASE with SUPORT1 and then calling it via STATSUB in another SUBCASE for buckling.
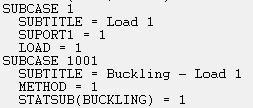
What am I doing wrong?
Photos of the setup.
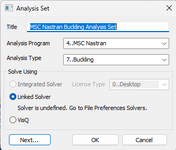
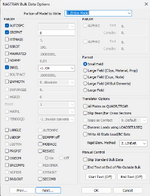
The model is a LAMINATE composite tube with two RBE3, each with a load in the center node. I put the SUPORT1 constraint in a random node restricting 123456 dofs, just for test.
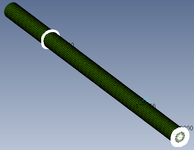
Here's the .nas/.dat Nastran file: https://drive.google.com/file/d/1RrH_hMMeLpE3qEWH_Ea3nuVQBoBBindj/view?usp=drivesdk
Here's the error I'm having in the buckling set, from the f06 file:

I have INREL set to -1 in the Bulk Data:
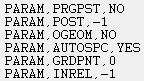
I also have SUPORT1 defined in the Bulk Data:

And finally I'm running a STATIC SUBCASE with SUPORT1 and then calling it via STATSUB in another SUBCASE for buckling.
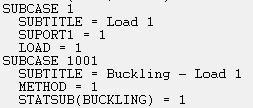
What am I doing wrong?
Photos of the setup.
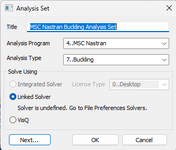
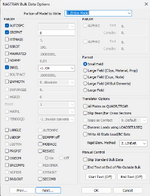
The model is a LAMINATE composite tube with two RBE3, each with a load in the center node. I put the SUPORT1 constraint in a random node restricting 123456 dofs, just for test.
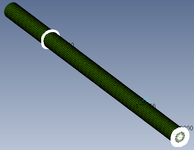
Attachments
Last edited: