Farhaad Shaik
Structural
Evening Colleagues,
Please can someone advise on how do I arrange the bolts at the splice position to transfer moment.
There is a very small moment but nevertheless needs to be catered for.
The structure is a steel bowstring pedestrian bridge that is envisaged to be put together on site.
No site welding is allowed therefore, the 4 truss segments are bolted together.
Can someone assist me with how to arrange the bolt connection at the diagonals, top and bottom transverse members as the current setup feels over designed.
The diagonal and top transverse members are 120x120x5 square hollow sections and the bottom transverse members are 150x150x8 square hollow sections.

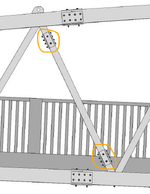
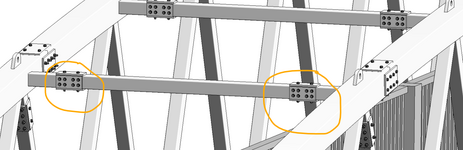
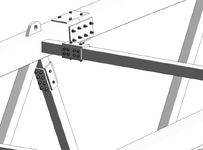
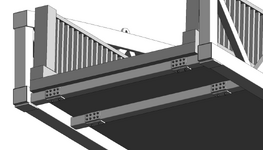
Please can someone advise on how do I arrange the bolts at the splice position to transfer moment.
There is a very small moment but nevertheless needs to be catered for.
The structure is a steel bowstring pedestrian bridge that is envisaged to be put together on site.
No site welding is allowed therefore, the 4 truss segments are bolted together.
Can someone assist me with how to arrange the bolt connection at the diagonals, top and bottom transverse members as the current setup feels over designed.
The diagonal and top transverse members are 120x120x5 square hollow sections and the bottom transverse members are 150x150x8 square hollow sections.

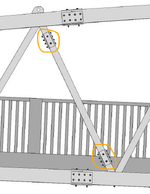
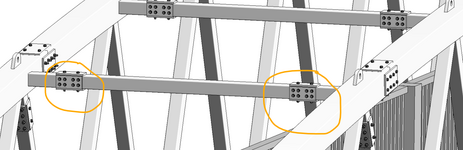
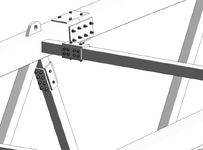
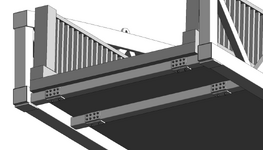