I often work on building designs in which the exterior structural steel is hidden inside a metal stud wall. This means that the cladding system consists of a continuous metal stud wall spanning vertically between each floor. The metal studs below the beam are framed into the bottom flange of a W-Shape and transfer wind load into the beam's bottom flange. This generates weak-axis bending and torsion in the beam. The top flange of the beam would be considered laterally braced by the floor or roof diaphragm. The beam would typically have a simple shear connection at each end, often a shear tab.
I'm curious to know how other engineers approach the design of this type of beam.All of the design examples I've seen for W-Shapes involve an eccentric vertical load that creates torsion and assumes the beam rotates about it's centroid. But in this specific case I would think the beam would rotate about the top flange. I've attached some example details for more clarification.
I'm curious to know how other engineers approach the design of this type of beam.All of the design examples I've seen for W-Shapes involve an eccentric vertical load that creates torsion and assumes the beam rotates about it's centroid. But in this specific case I would think the beam would rotate about the top flange. I've attached some example details for more clarification.
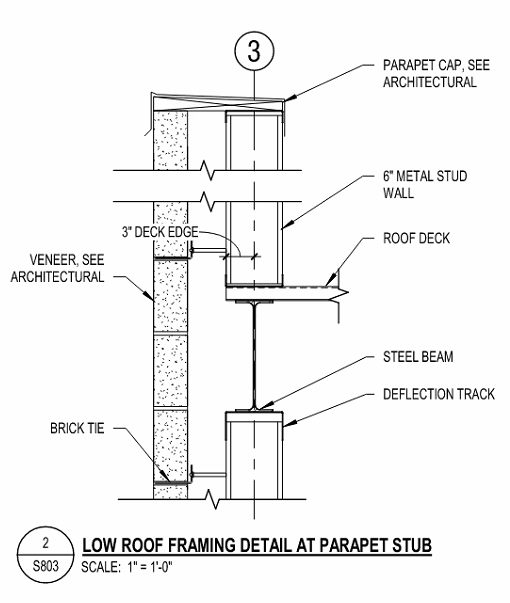
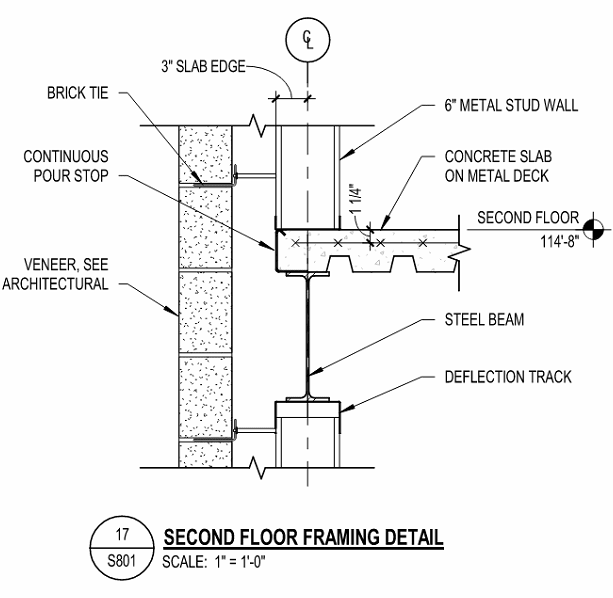