Mech5656
Mechanical
- Aug 2, 2014
- 127
Hello,
I work for a pump repair shop and recently we received a cover for pump (BB2 type pump).The service is HF acid and therefore I think we have this issues. The pump service pressure is 800 psi and temp is 95F. Cover base material is carbon steel with monel welding on registers. Initially, the welding was sticking out and we decided to machine off 0.020" from monel welding and weld on top on it. After machining, and during welding, we found that there are hydrocarbon pockets and we couldnt weld it. We machined more and remove all monel and now we will be welding on carbon steel with nickel butter pass and then monel weld. Here are few pictures. Please provide your feedback on what would be the best way to weld this? Would baking this part at 700F help? What else we can do better? Is baking necessary and will help?
pre-machining
Unable to weld
I work for a pump repair shop and recently we received a cover for pump (BB2 type pump).The service is HF acid and therefore I think we have this issues. The pump service pressure is 800 psi and temp is 95F. Cover base material is carbon steel with monel welding on registers. Initially, the welding was sticking out and we decided to machine off 0.020" from monel welding and weld on top on it. After machining, and during welding, we found that there are hydrocarbon pockets and we couldnt weld it. We machined more and remove all monel and now we will be welding on carbon steel with nickel butter pass and then monel weld. Here are few pictures. Please provide your feedback on what would be the best way to weld this? Would baking this part at 700F help? What else we can do better? Is baking necessary and will help?
pre-machining
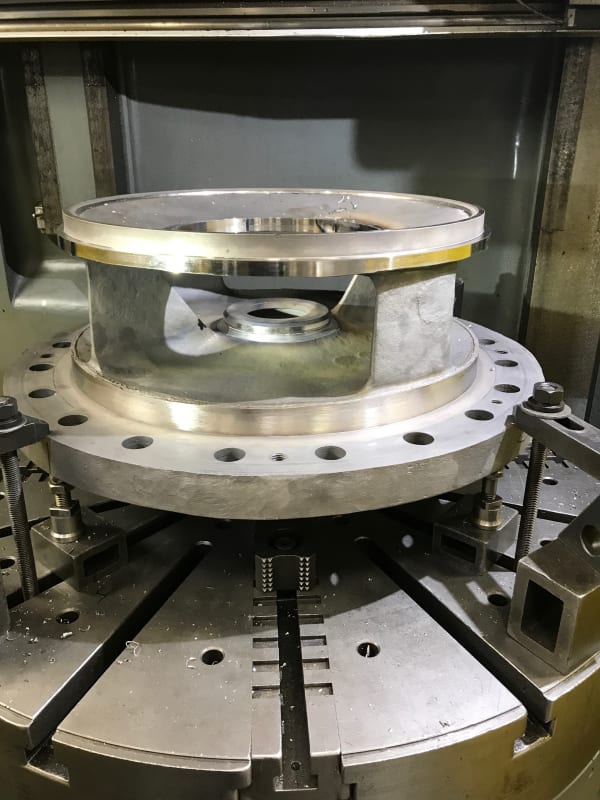
Unable to weld
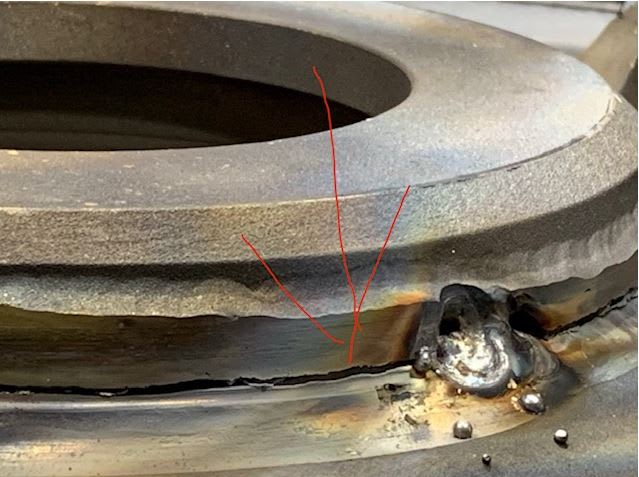
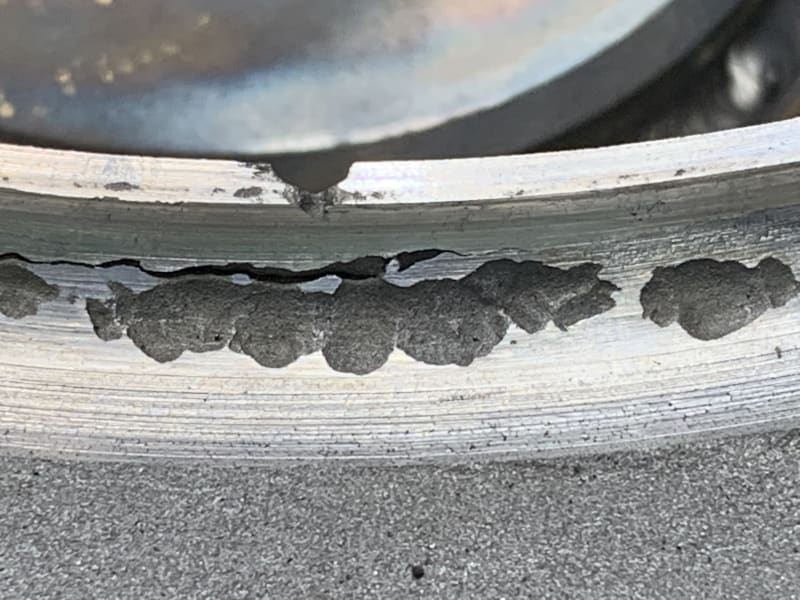