Hi,
I would like to conduct a frequency analysis on the following fin in Abaqus.
In the mesh module > mesh controls Abaqus only lets me use a Tet mesh (or a bottom up Hex). However, if I mesh with tetrahedral elements I get a very bad aspect ratio for the elements on the leading edge of the fin geometry
Making the mesh finer reduces the aspect ratio, but is not a viable solution because it would need to be incredibly fine. If I run the simulation I get the error that these elements are distorted.
How should I attempt to solve this issue / what is the best way to mesh this part? Would this issue be resolved with hexahedral elements? Can the geometry be partitioned?
My thinking is that the edge is so thin and that is causing the huge aspect ratio.
Thank you.
I would like to conduct a frequency analysis on the following fin in Abaqus.
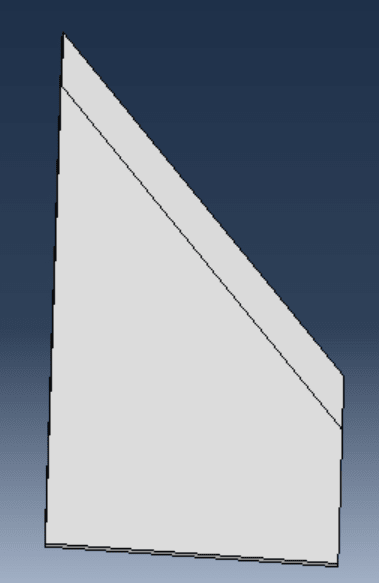
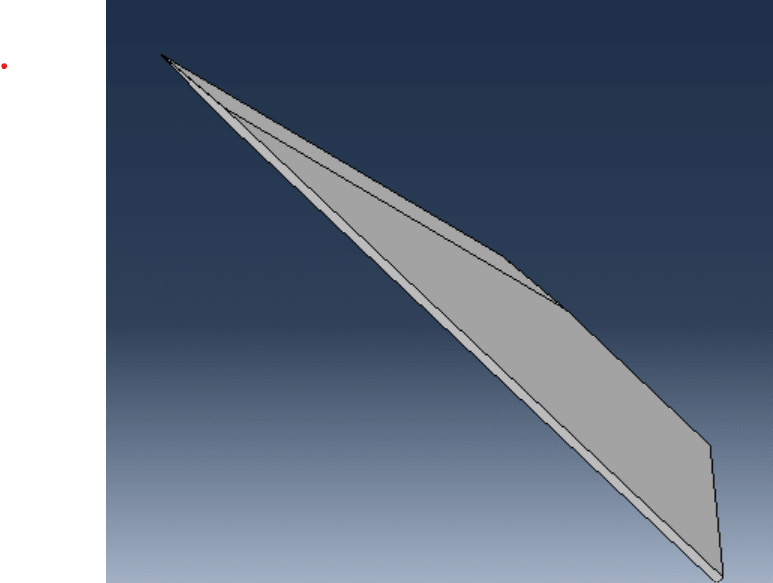
In the mesh module > mesh controls Abaqus only lets me use a Tet mesh (or a bottom up Hex). However, if I mesh with tetrahedral elements I get a very bad aspect ratio for the elements on the leading edge of the fin geometry
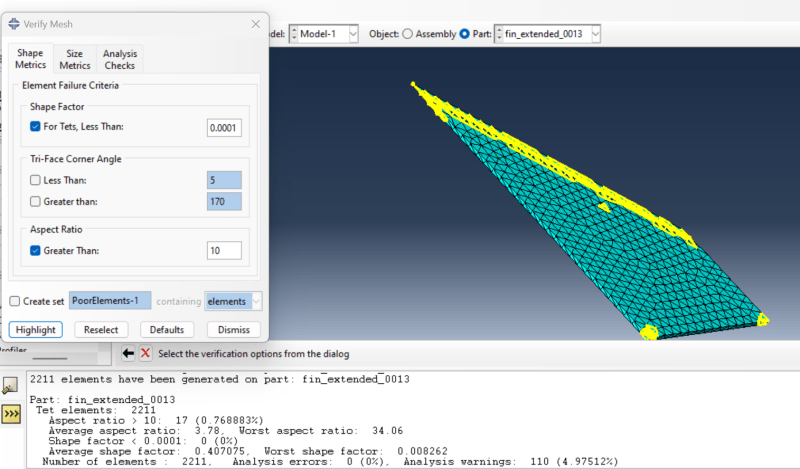
Making the mesh finer reduces the aspect ratio, but is not a viable solution because it would need to be incredibly fine. If I run the simulation I get the error that these elements are distorted.
How should I attempt to solve this issue / what is the best way to mesh this part? Would this issue be resolved with hexahedral elements? Can the geometry be partitioned?
My thinking is that the edge is so thin and that is causing the huge aspect ratio.
Thank you.