ViaParadise
Structural
I am modelling a built up HSS section where there is a thickness change of the flanges along its length. This is done by keeping the flanges flush on the outer side resulting in a vertical eccentricity between the centerlines of the flanges. Modelling this (and just considering the free-body diagram) results in a deflected shape like shown in the image below when the section is subject to axial compression loading on the thin side. The shape and curvature makes sense.
However, the bending stresses do not. It seems as though the tension side of the thinner and thicker plate actually have an increased compressive bending stress. My assumption is that the axial compressive stress + bending compressive stress (on the compression side) would be larger than on the side of the flanges that are elongating due to this eccentricity induced bending.
After speaking about this with others we cannot seem to find a clear reason for this.
For reference, we've tried the following:
-Modelling only the top flange with a fixity on the thicker side produces an expected result of the outer side being in compression and inner side in tension but this also assumes the thin side of the flange can move freely when it is actually restrained by the beam webs.
-Adjusting different types of offsets, i.e. modelling the plates on their top surface vs center surface and adjust geometry in the model and loading and support conditions, the results do not change.
-Modelling simply as 2 beam elements with different thicknesses and vertically offset with a ramp at the transition, again results are confusingly the same.
Any ideas on what may be wrong? We're currently assuming it's not the model but our intuition of what is actually happening, that is looking for an explanation which is a difficult endeavor. I've also started looking at reverse fault lines in geology as they seem to show this behavior but have struggled to find any good explanation of the stresses and an explanation for them.

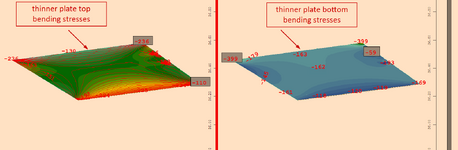
However, the bending stresses do not. It seems as though the tension side of the thinner and thicker plate actually have an increased compressive bending stress. My assumption is that the axial compressive stress + bending compressive stress (on the compression side) would be larger than on the side of the flanges that are elongating due to this eccentricity induced bending.
After speaking about this with others we cannot seem to find a clear reason for this.
For reference, we've tried the following:
-Modelling only the top flange with a fixity on the thicker side produces an expected result of the outer side being in compression and inner side in tension but this also assumes the thin side of the flange can move freely when it is actually restrained by the beam webs.
-Adjusting different types of offsets, i.e. modelling the plates on their top surface vs center surface and adjust geometry in the model and loading and support conditions, the results do not change.
-Modelling simply as 2 beam elements with different thicknesses and vertically offset with a ramp at the transition, again results are confusingly the same.
Any ideas on what may be wrong? We're currently assuming it's not the model but our intuition of what is actually happening, that is looking for an explanation which is a difficult endeavor. I've also started looking at reverse fault lines in geology as they seem to show this behavior but have struggled to find any good explanation of the stresses and an explanation for them.

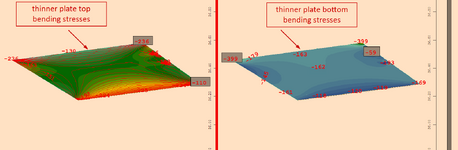
Last edited: