Hi guys,
I am trying to simulate and measure the rotation of the horizontal beam wrt to the vertical column on a beam-column joint after loading. There are two independent variables, (1) the vertical load of applied on the beam (0-20kN) and (2) the predefined temperature of the whole structure (0-800 degrees celcius). The measured variable is the rotation, and the problem is static (the load & temperature is not cyclical). To model the temperature we have changed the plasticity of the whole structure.
PROBLEM: Currently I am trying to run the simulation at high temperatures (of around 500 degrees celcius) and loads of around 20kN, however the model gets stuck at roughly 48% of the load applied and then aborts due to an error. Any ideas what may be wrong?
I believe the problem may be within the contact definition as some of the warnings given were to do with the contact. Here is the warning dialog given from the simulation. I've given some detail about my assembly below.
THE SLAVE SURFACES ASSEMBLY_CP-2-BOLT-1 AND ASSEMBLY_CP-3-BOLT-1 INTERSECT EACH OTHER. THEY ARE PAIRED WITH MASTER SURFACES ASSEMBLY_CP-2-QUARTERCOLUMN-1 AND ASSEMBLY_CP-3-QUARTERCOLUMN-1 THAT ALSO INTERSECT EACH OTHER. IF BOTH PAIRS ARE *CONTACT PAIRs, THESE TWO PAIRS SHOULD NOT BE SIMULTANEOUSLY PRESENT IN A STEP BECAUSE OF POSSIBLE CONVERGENCE PROBLEMS; USE *MODEL CHANGE,TYPE=CONTACT PAIR TO REMOVE ONE OF THEM. IF BOTH ARE *TIE PAIRS, THE REDUNDANT TIES WILL BE REMOVED AUTOMATICALLY. IF ONE PAIR IS *TIE AND ANOTHER IS *CONTACT PAIR, REMOVE ONE OF THEM.
For contact pair (assembly_cp-1-quarterweldedthickplate-1-assembly_cp-1-quartercolumn-1), adjustment was specified but no node was adjusted more than the adjustment distance = 2.22000e-16.
For contact pair (assembly_cp-2-bolt-1-assembly_cp-2-quartercolumn-1), adjustment was specified but no node was adjusted more than the adjustment distance = 2.22000e-16.
Not all the nodes that do not find intersection with the master surface are printed. However all of these nodes have been included in a node set.
*************************************
Below is a picture of the assembly. So I have three components - (1) The Beam which has a welded plate (2) Bolts (3) Column. I have defined interactions between them with friction coefficient of 0.1 and hard contact. Using the interactions > find contact pairs, ABAQUS found the pairs automatically and assigned the slave/master surface accordingly. For all of them I used small sliding, and adjust the slave only to remove overclosure.
I am trying to simulate and measure the rotation of the horizontal beam wrt to the vertical column on a beam-column joint after loading. There are two independent variables, (1) the vertical load of applied on the beam (0-20kN) and (2) the predefined temperature of the whole structure (0-800 degrees celcius). The measured variable is the rotation, and the problem is static (the load & temperature is not cyclical). To model the temperature we have changed the plasticity of the whole structure.
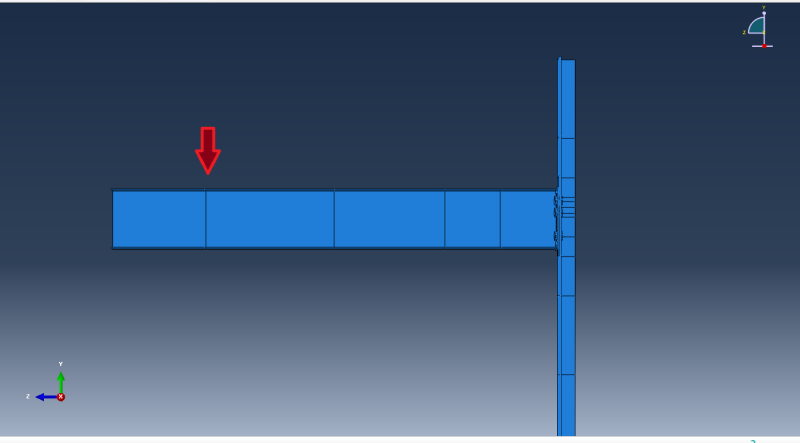
PROBLEM: Currently I am trying to run the simulation at high temperatures (of around 500 degrees celcius) and loads of around 20kN, however the model gets stuck at roughly 48% of the load applied and then aborts due to an error. Any ideas what may be wrong?
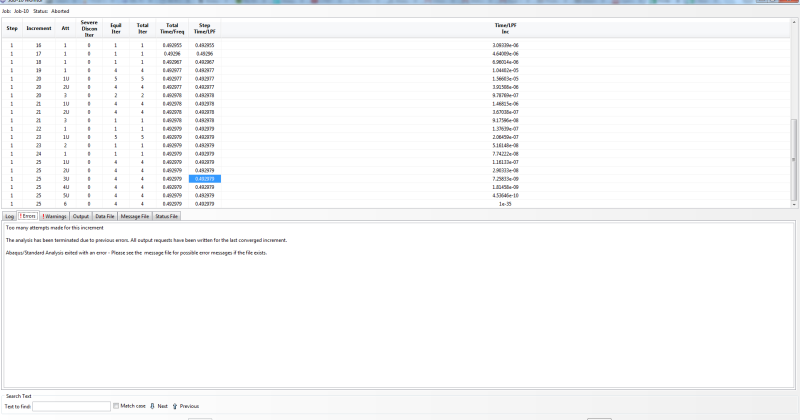
I believe the problem may be within the contact definition as some of the warnings given were to do with the contact. Here is the warning dialog given from the simulation. I've given some detail about my assembly below.
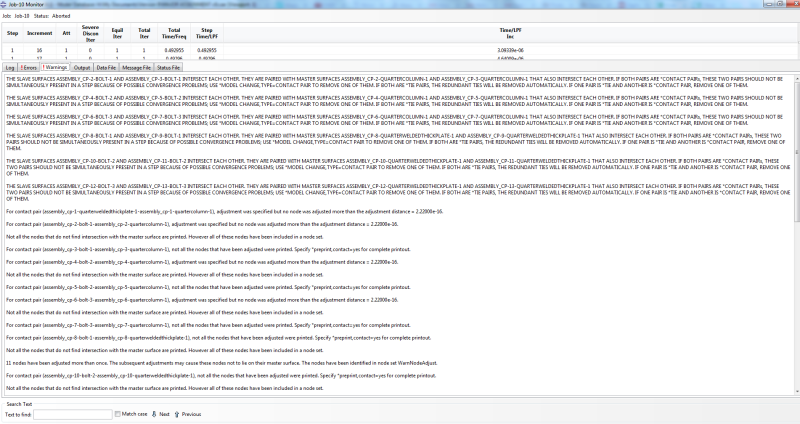
THE SLAVE SURFACES ASSEMBLY_CP-2-BOLT-1 AND ASSEMBLY_CP-3-BOLT-1 INTERSECT EACH OTHER. THEY ARE PAIRED WITH MASTER SURFACES ASSEMBLY_CP-2-QUARTERCOLUMN-1 AND ASSEMBLY_CP-3-QUARTERCOLUMN-1 THAT ALSO INTERSECT EACH OTHER. IF BOTH PAIRS ARE *CONTACT PAIRs, THESE TWO PAIRS SHOULD NOT BE SIMULTANEOUSLY PRESENT IN A STEP BECAUSE OF POSSIBLE CONVERGENCE PROBLEMS; USE *MODEL CHANGE,TYPE=CONTACT PAIR TO REMOVE ONE OF THEM. IF BOTH ARE *TIE PAIRS, THE REDUNDANT TIES WILL BE REMOVED AUTOMATICALLY. IF ONE PAIR IS *TIE AND ANOTHER IS *CONTACT PAIR, REMOVE ONE OF THEM.
For contact pair (assembly_cp-1-quarterweldedthickplate-1-assembly_cp-1-quartercolumn-1), adjustment was specified but no node was adjusted more than the adjustment distance = 2.22000e-16.
For contact pair (assembly_cp-2-bolt-1-assembly_cp-2-quartercolumn-1), adjustment was specified but no node was adjusted more than the adjustment distance = 2.22000e-16.
Not all the nodes that do not find intersection with the master surface are printed. However all of these nodes have been included in a node set.
*************************************
Below is a picture of the assembly. So I have three components - (1) The Beam which has a welded plate (2) Bolts (3) Column. I have defined interactions between them with friction coefficient of 0.1 and hard contact. Using the interactions > find contact pairs, ABAQUS found the pairs automatically and assigned the slave/master surface accordingly. For all of them I used small sliding, and adjust the slave only to remove overclosure.
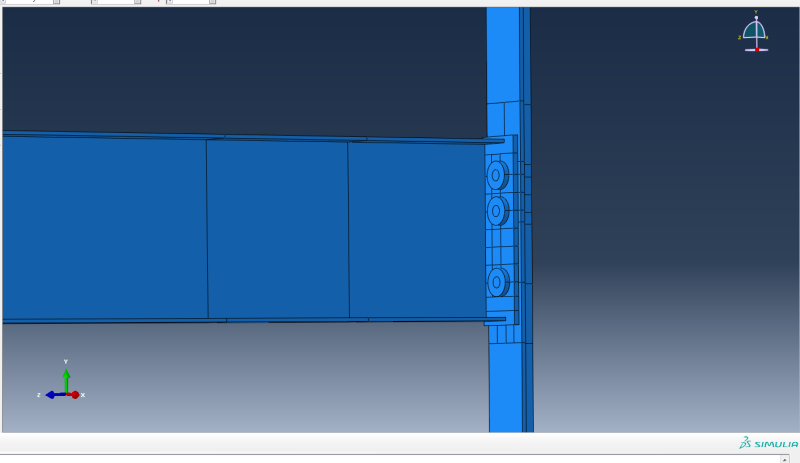
