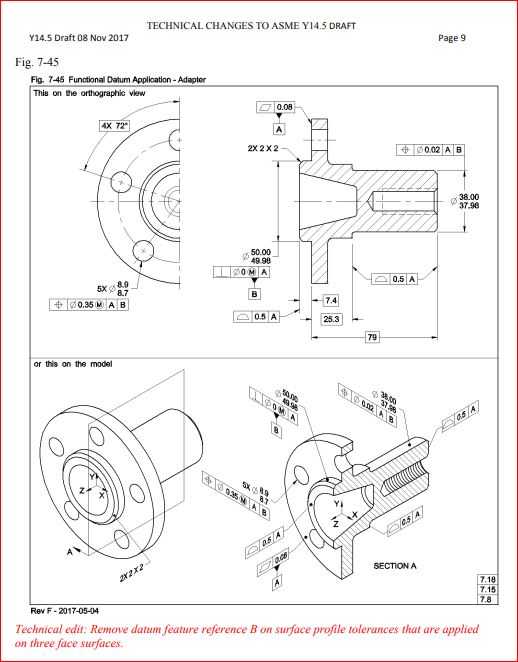
ASME Y14.5-2009 figure 4-38 has "B" as secondary in the profile callout for the planar surfaces (three face surfaces)
The new version 2018 of the same standard removed "B" intentionally -- as clearly shown in the technical changes draft --document attached.
Does anyone of the members of this forum (maybe committee members or just GDT passionate) have some ideas on why this change has been done?
What could be a good reason?
Does not look like just a clerical change/ mistake/ typo or an unintentional change... ( as 2x 2 x 2 for the end face chamfer instead of 2x 2X45° probably is)
Any input will be greatly appreciated.