cal91
Structural
- Apr 18, 2016
- 294
There is no other axial load in the HSS member.
There are two stiffeners that align with the HSS8x4x1/2 walls (4" apart) The welds are vertical between the angle and the HSS8x4x1/2. As such, all of the load should be directly transmitted into the web walls of the HSS, and there will be no chord plastification.
As long as the welds, angle, and stiffeners are adequate, am I wrong in stating that the strength of this connection is the full capacity of the HSS8x4 member (axial-single bending interaction)?
There are two stiffeners that align with the HSS8x4x1/2 walls (4" apart) The welds are vertical between the angle and the HSS8x4x1/2. As such, all of the load should be directly transmitted into the web walls of the HSS, and there will be no chord plastification.
As long as the welds, angle, and stiffeners are adequate, am I wrong in stating that the strength of this connection is the full capacity of the HSS8x4 member (axial-single bending interaction)?
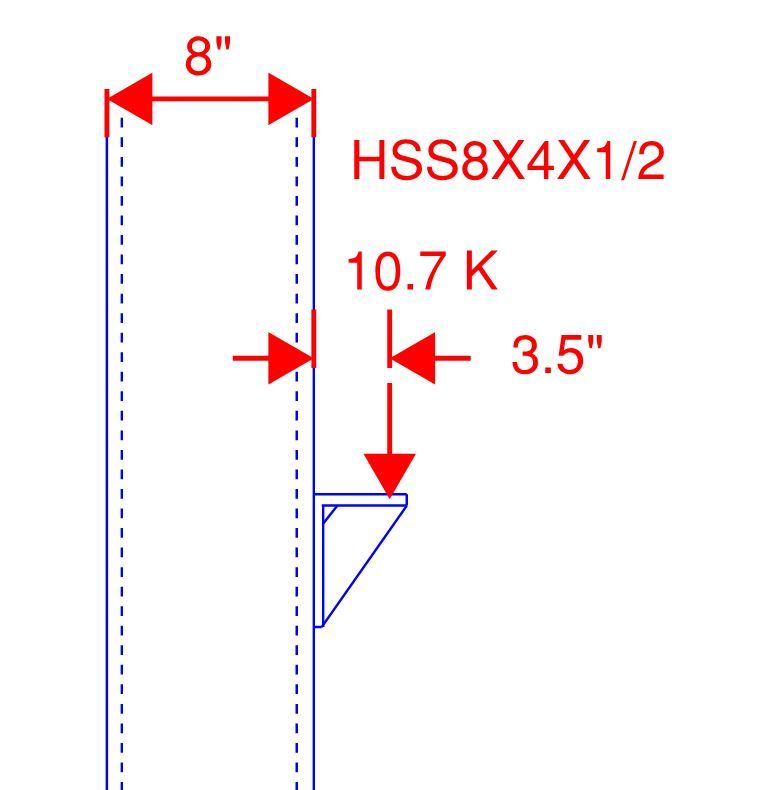