RDelaCourt513
Mechanical
Hi all,
I am a relatively new Ansys user and am currently analysing a space frame chassis with means of exploring the structure deformation upon impact of rigid surface.
I have created the chassis by using the 'weldment' feature on Solidworks and imported the Solidworks assembly (chassis and wall) into ANSYS Mechanical. (For the initial study I have only included a section of the Rollcage so I can understand what it is that I am doing first before I go deeper).
Why is my mesh in the form that is shown in picture 2 where a combination of mesh elements are used? Is there a better way to set up the mesh? (tubes are hollow (30mm OD,2.5 Thick)). Would it be easier to shell model the chassis?
Lastly (and I really would appreciate this a response to this) Can someone explain to me how I should set up the 'step controls' (max no. of cycles, End Time, Initial time step, Min time step and max time step.
Currently my solver times are ridiculous, For the entire Rollcage geometry in this explicity dynamics solver with everything set to 'programme controlled', the study is expected to take 100 hours.
AMD FX(tm) - 8350 Eight core processor
16Gb Ram
velocity is going to be set to 50,000mm/s
Thank you guys in advance and I apologise, In the past I have always researched what to do before seeking help but I am in a rush with this and time is starting to get the better of me.
Thank you,
Ryan.
I am a relatively new Ansys user and am currently analysing a space frame chassis with means of exploring the structure deformation upon impact of rigid surface.
I have created the chassis by using the 'weldment' feature on Solidworks and imported the Solidworks assembly (chassis and wall) into ANSYS Mechanical. (For the initial study I have only included a section of the Rollcage so I can understand what it is that I am doing first before I go deeper).
Why is my mesh in the form that is shown in picture 2 where a combination of mesh elements are used? Is there a better way to set up the mesh? (tubes are hollow (30mm OD,2.5 Thick)). Would it be easier to shell model the chassis?
Lastly (and I really would appreciate this a response to this) Can someone explain to me how I should set up the 'step controls' (max no. of cycles, End Time, Initial time step, Min time step and max time step.
Currently my solver times are ridiculous, For the entire Rollcage geometry in this explicity dynamics solver with everything set to 'programme controlled', the study is expected to take 100 hours.
AMD FX(tm) - 8350 Eight core processor
16Gb Ram
velocity is going to be set to 50,000mm/s
Thank you guys in advance and I apologise, In the past I have always researched what to do before seeking help but I am in a rush with this and time is starting to get the better of me.
Thank you,
Ryan.
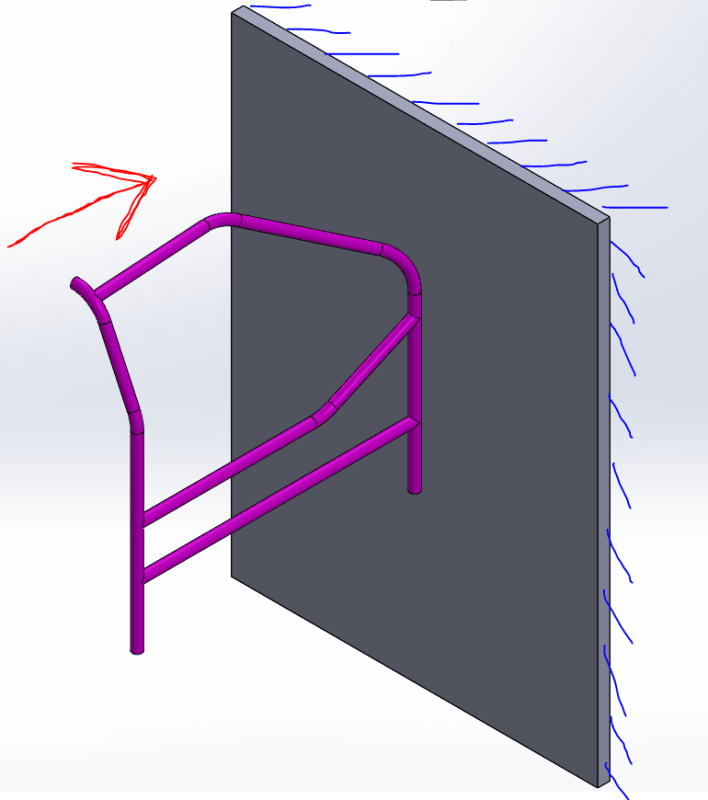
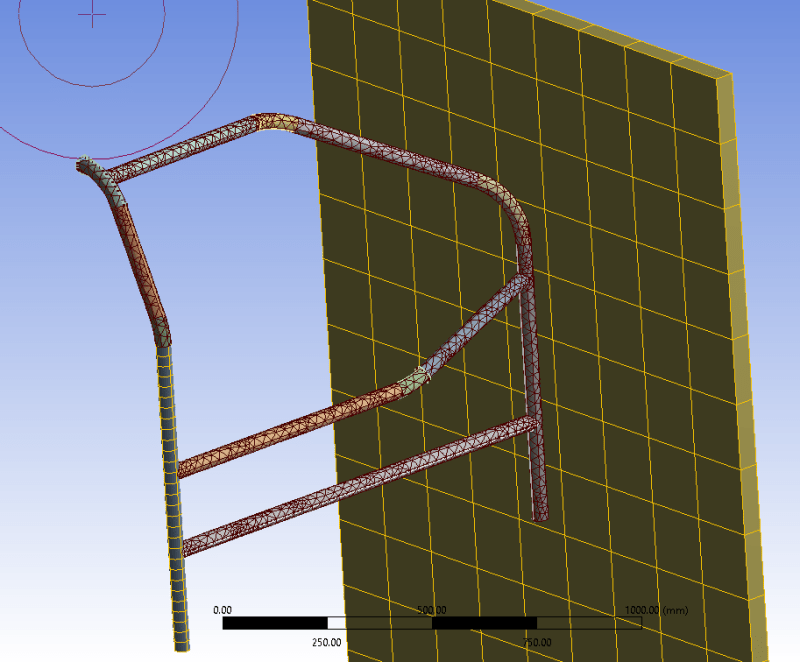
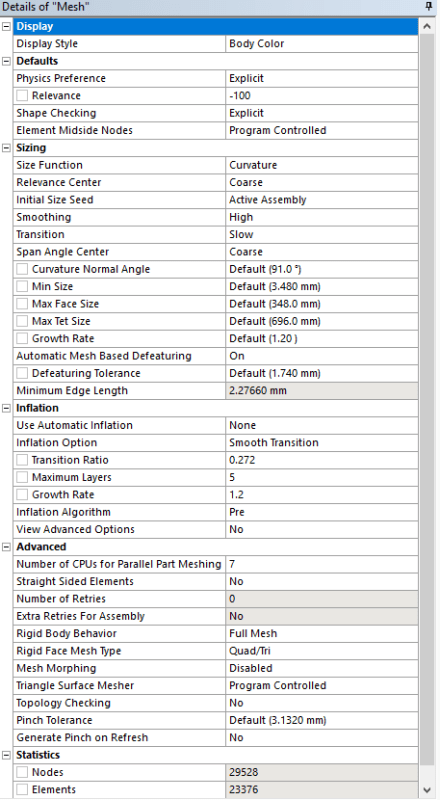