Hi Friends, I am a beginner in the Abaqus and trying to understand the impact of different heat source on the metal plate. For the current case, I am using Gaussian distribution heat source to simulate the melting in the Ti plate. So my thermal model uses temperature-dependent specific heat, conductivity, latent heat and density. Also, the sample size of 0.8X0.8X0.4mm with the mesh size of 0.8/200. To give desired surface heat flux I am using DFLUX subroutine.
My units look consistent, I am using the metric standard where my conductivity varies from 4 to 40 W/mK wrt temp, Density 4400Kg/m3, specific heat order of 750 below MP and 950 J/Kg-K after MP. Attributes consider 0 K temperature and metric Boltzmann constant 5.67*10-8.
My model considers 70-watt Gaussian power with an effective diameter of 125micro-meter for 400 microseconds. Therefore I cannot change my maximum time increment beyond 400us. I am using DC3D8: An 8-node linear heat transfer brick.
Now the problem I am facing is the following:
1. The surface of model is exposed to a very high temperature but the temperature is not conducting to the next layer of nodes, please check the image. I read some journal where they reported that the depth of melting goes up to 120-200micron. My simulation shows just 2 microns. I have to know where I am doing wrong.
2. Simulation is not completing, either it says time step is too big (for fixed time step) or it says Too many attempts made for this increment (Automatic steps). I used other time steps and mesh size it solves but I don't know what I am doing and why I am doing? If you can explain or give some reference from where I can read and learn how to adjust the step size?.
My units look consistent, I am using the metric standard where my conductivity varies from 4 to 40 W/mK wrt temp, Density 4400Kg/m3, specific heat order of 750 below MP and 950 J/Kg-K after MP. Attributes consider 0 K temperature and metric Boltzmann constant 5.67*10-8.
My model considers 70-watt Gaussian power with an effective diameter of 125micro-meter for 400 microseconds. Therefore I cannot change my maximum time increment beyond 400us. I am using DC3D8: An 8-node linear heat transfer brick.
Now the problem I am facing is the following:
1. The surface of model is exposed to a very high temperature but the temperature is not conducting to the next layer of nodes, please check the image. I read some journal where they reported that the depth of melting goes up to 120-200micron. My simulation shows just 2 microns. I have to know where I am doing wrong.
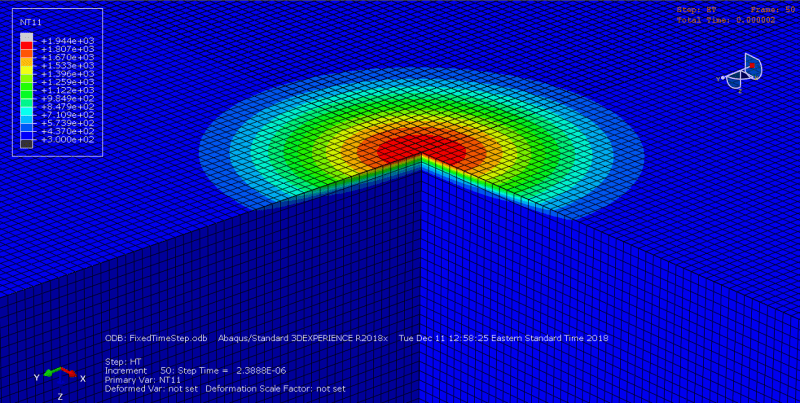
2. Simulation is not completing, either it says time step is too big (for fixed time step) or it says Too many attempts made for this increment (Automatic steps). I used other time steps and mesh size it solves but I don't know what I am doing and why I am doing? If you can explain or give some reference from where I can read and learn how to adjust the step size?.
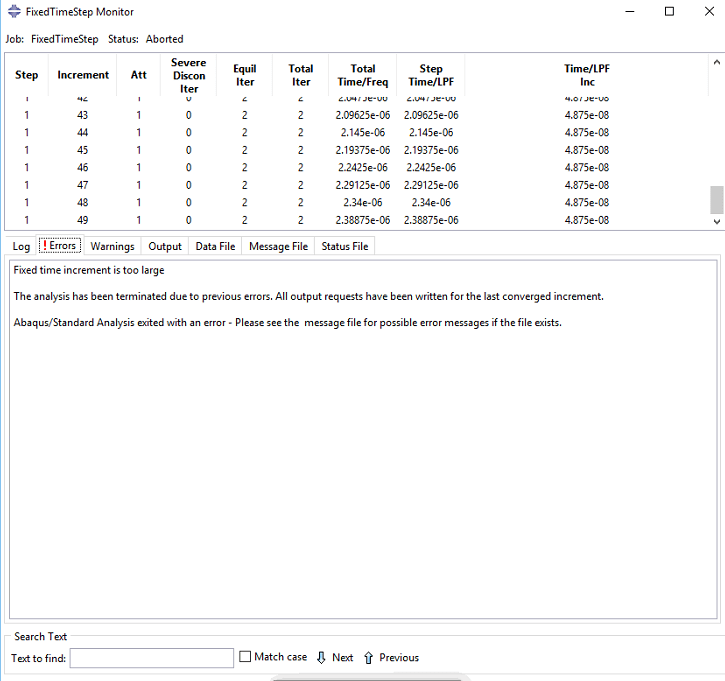
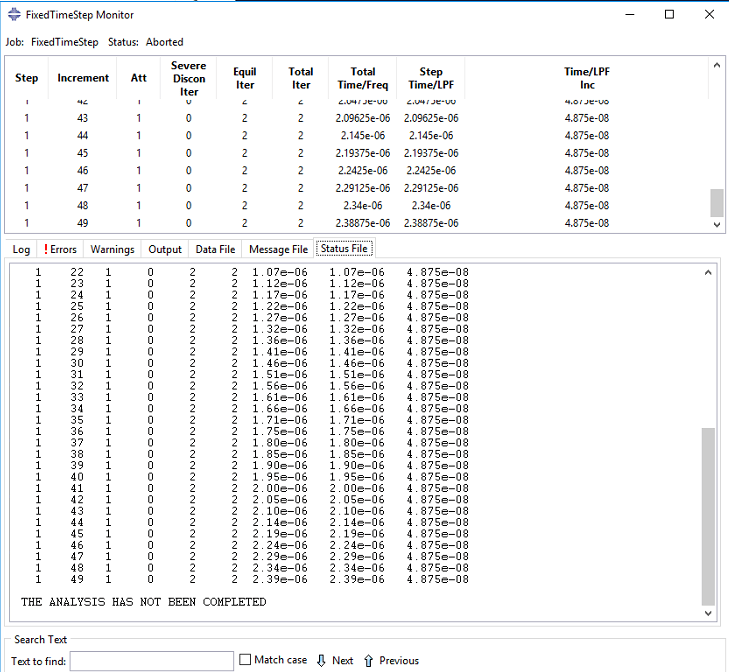