We're working on a project to roll thread some solution annealed 718 and have run into issues with lap formation. The parts are roll threaded in an infeed setup using a 2-die roller machine (setup picture below.) The dies are 6" long and close in on a 5" machined blank with chamfered ends. After completing threading, we ran liquid penetrant testing and noted issues on the threads flanks. A lap has folded halfway up the thread flank and wraps all the way around the thread for the full length of the 5" threaded region. The lap doesn't show on all pieces (approximately 20% defect rate) nor is it consistent on what side of the flank the lap shows up on (forward or aft of machine.)
I took a cross section of the thread and examined it under magnification. Below are pictures at 50x and stitched together thread profiles. The lap appears to begin to form in the chamfered region of the machine blank and wraps around to the fully formed thread. I'm at a bit of a loss as to what could be causing the lap to form in the chamfered region then roll up. Historically, I've seen issues in thread mismatch of the dies, thread blank leveling, die condition, etc. but these variables have all been checked.
718 is known to form 'funny' compared to our bread & butter low alloy steels. In low alloy it's pretty consistent that if you push the thread with a die, material moves in a manner that you would expect. 718 we have found the material will resist forming and, when filling voids like on a roll thread or forming die, will sometimes burst causing issues. In previous projects, I've learned that 718 resists forming at speeds that typical low alloy steel would have no issues with forming. That said, I'm still having difficulty imagining the force profile that would create the below laps.
What thoughts are out there that could be forming this?
Does anyone have any literature out there?
50x metallography, material chamfer begins on left side and grows upward. -
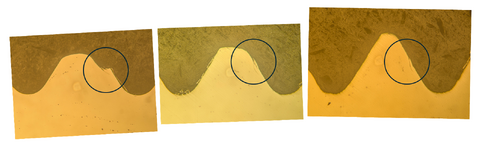
2-die infeed setup (no affiliation, borrowed from google images)
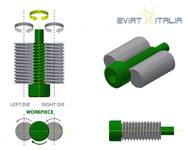
I took a cross section of the thread and examined it under magnification. Below are pictures at 50x and stitched together thread profiles. The lap appears to begin to form in the chamfered region of the machine blank and wraps around to the fully formed thread. I'm at a bit of a loss as to what could be causing the lap to form in the chamfered region then roll up. Historically, I've seen issues in thread mismatch of the dies, thread blank leveling, die condition, etc. but these variables have all been checked.
718 is known to form 'funny' compared to our bread & butter low alloy steels. In low alloy it's pretty consistent that if you push the thread with a die, material moves in a manner that you would expect. 718 we have found the material will resist forming and, when filling voids like on a roll thread or forming die, will sometimes burst causing issues. In previous projects, I've learned that 718 resists forming at speeds that typical low alloy steel would have no issues with forming. That said, I'm still having difficulty imagining the force profile that would create the below laps.
What thoughts are out there that could be forming this?
Does anyone have any literature out there?
50x metallography, material chamfer begins on left side and grows upward. -
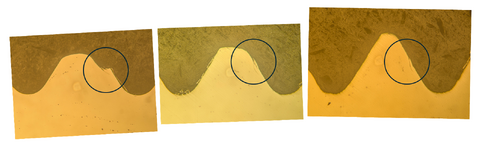
2-die infeed setup (no affiliation, borrowed from google images)
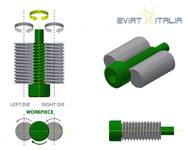