Hello everyone,
I’m working on a welded connection between a rectangular hollow section (RHS) beam and a flat rectangular plate.
The RHS is fixed on one end, and on the other end, a flat plate is fillet-welded around its perimeter (full weld) to the open face of the RHS.
The flat plate is intended to be pulled downward, perpendicular to the beam’s axis – generating axial tension on the plate and corresponding load on the welds.
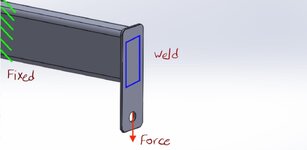
I’m looking for guidance on how to calculate the minimum weld throat size required in this configuration.
I’m working on a welded connection between a rectangular hollow section (RHS) beam and a flat rectangular plate.
The RHS is fixed on one end, and on the other end, a flat plate is fillet-welded around its perimeter (full weld) to the open face of the RHS.
The flat plate is intended to be pulled downward, perpendicular to the beam’s axis – generating axial tension on the plate and corresponding load on the welds.
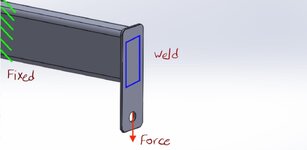
I’m looking for guidance on how to calculate the minimum weld throat size required in this configuration.