MacMcMacmac
Aerospace
Hello. I was wondering if there is an approved method of cleaning centrifugal compressor rotors while in service. Our main 8MW compressor is once again experiencing a build up of material on the 4th stage impeller due to a leak in the 3rd to 4th stage intercooler. The corrosion inhibitor is precipitating out of the water stream and is mixing with soot particles in the air stream to form a hard, chalky residue on the blades. What is unfortunate, is that we just completed this repair less than 2 weeks ago. A new leak has apparently formed in the tube nest and is creating the same problem. This is a 40 year old Ingersoll Rand/Dresser rand unit that is acting as a large exhauster for an engine test cell. The airflow though the unit ranges from 7 to 30lbs/sec, which is actually fairly low compared to its design potential, so I am thinking velocity through the unit is probably not terribly high.
This is the final stage and is discharging to atmosphere, so any residue it discharges will be going down the line and to the stack.
Getting the volute off was not easy as it was corroded on very tight to the gearcase spigot. We initially attempted to remove the inlet cone from the volute, but it is a two piece affair, and once the outer cone was off, the amount of corrosion discovered on the inner bolts, housing and alignment screws convinced us just taking the whole volute off was the simpler route.
If there was a way to dissolve this build up while in service, it could allow us to continue in operation during critical testing timeframe commitments. We are 2 weeks off from our annual shutdown, so it looks like we will go with the manual route for now. New tube nests are under construction and are scheduled to arrive about 2 weeks after our shutdown has finished (naturally). Unfortunately, due to changes in the piping codes since the original tube nests were constructed, the new tube sheets have to be an inch thicker, which will necessitate raising the cooling water supply and return piping network by an inch. Fun times.
I manually cleaned the impeller and it took 5 1/2 hrs to get it all off.
This is the final stage and is discharging to atmosphere, so any residue it discharges will be going down the line and to the stack.
Getting the volute off was not easy as it was corroded on very tight to the gearcase spigot. We initially attempted to remove the inlet cone from the volute, but it is a two piece affair, and once the outer cone was off, the amount of corrosion discovered on the inner bolts, housing and alignment screws convinced us just taking the whole volute off was the simpler route.
If there was a way to dissolve this build up while in service, it could allow us to continue in operation during critical testing timeframe commitments. We are 2 weeks off from our annual shutdown, so it looks like we will go with the manual route for now. New tube nests are under construction and are scheduled to arrive about 2 weeks after our shutdown has finished (naturally). Unfortunately, due to changes in the piping codes since the original tube nests were constructed, the new tube sheets have to be an inch thicker, which will necessitate raising the cooling water supply and return piping network by an inch. Fun times.
I manually cleaned the impeller and it took 5 1/2 hrs to get it all off.
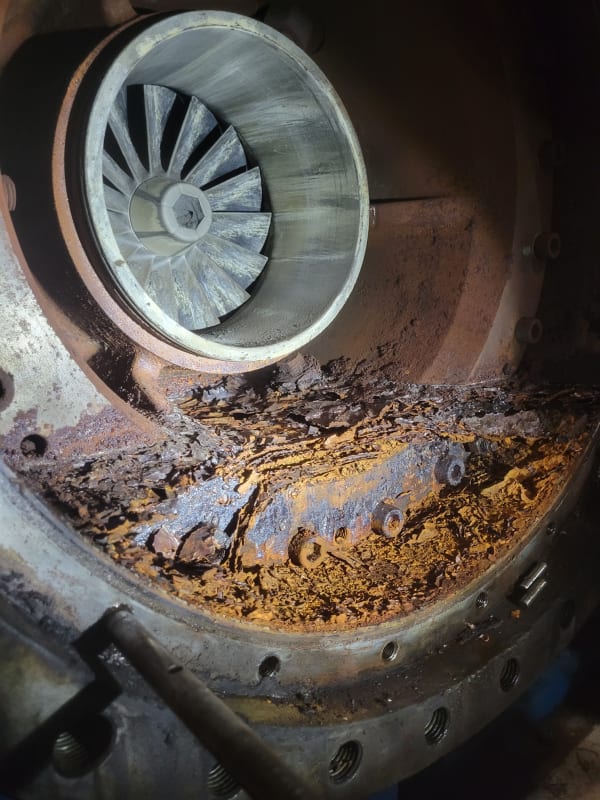
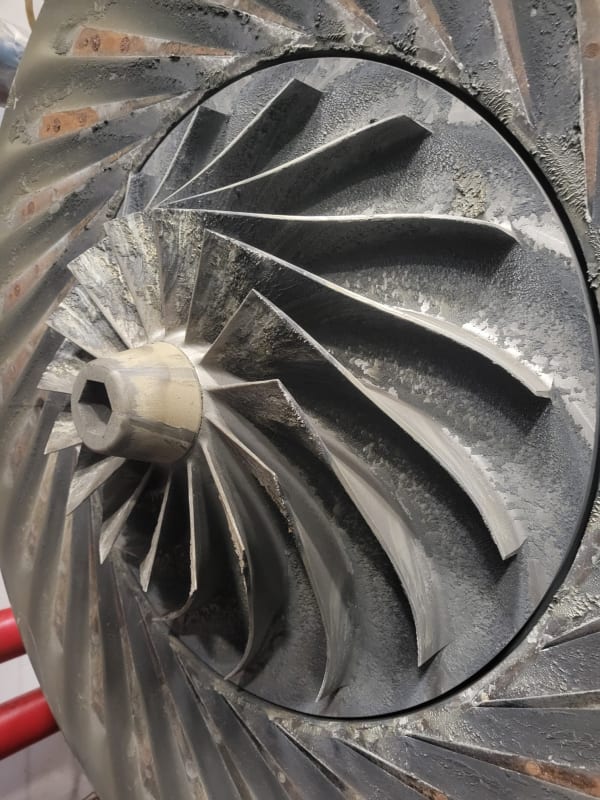
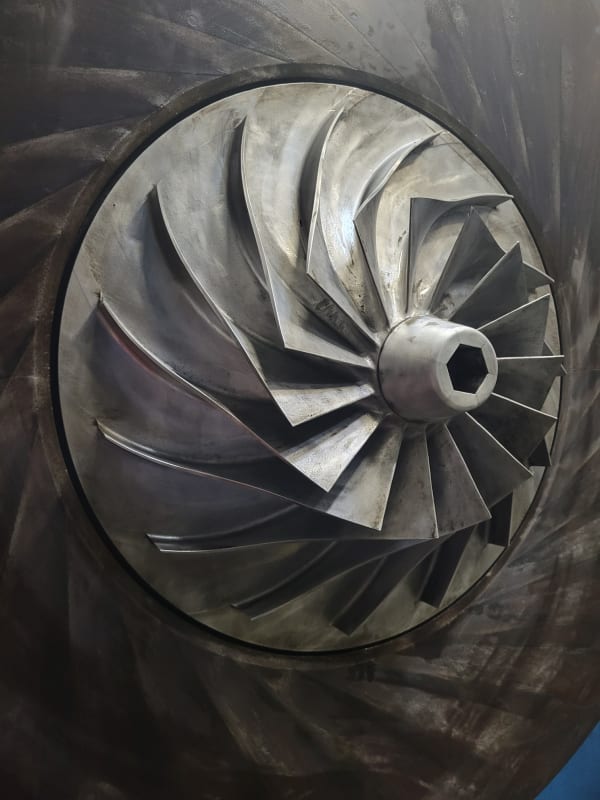