I have a technical challenge, where I need to properly evaluate the axial force of the cylinder (D) rolling on two rollers (d). Data of axial force is needed, because I need to properly design the front and back stopper for the pipe. And because of lack of space (too much to explain here) it is necessary to properly evaluate the force so I don't overdimension the stoppers.
The reason that axial force comes into play is that the big cylinder (D) can be a bit conically shaped. Cylinder (D), in my case, is a pipe with a maximum diameter of 4000 mm and a mass of around 10.000 kg.
Can anyone please point me in the proper direction on how to evaluate this, or have any similar problems known that I can build on?
The reason that axial force comes into play is that the big cylinder (D) can be a bit conically shaped. Cylinder (D), in my case, is a pipe with a maximum diameter of 4000 mm and a mass of around 10.000 kg.
Can anyone please point me in the proper direction on how to evaluate this, or have any similar problems known that I can build on?
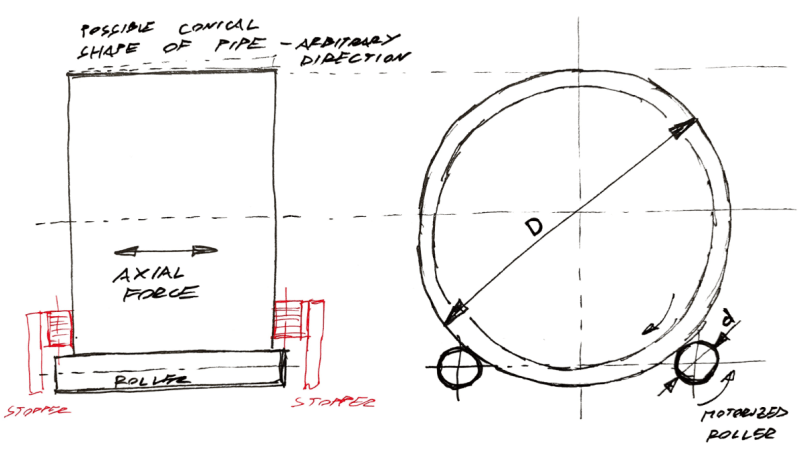