Hello everybody,
I want to ask about the bolting on industrial hydrogen electrolysers.
These systems can have 150+ cells bolted together with a single bolting system, to create a stack.
Each cell of the stack are sealed with a gasket of some sort. EPDM, Viton, PTFE etc..
Generally a low internal pressure is present say max 1 bar, and temps upto 90°C.
Example image of an industrial stack, check out the crazy bolting!
Now normal calculations for a bolted flange joint are for single gasket systems.
How valid is it to use these calculations with a stack of 150 gaskets..
What additional assumptions are we making when stacking 150 of them together.. i.e. does the stress really translate evenly through the whole stack ?
Then how on earth do you load this evenly, many people fail to load a single gasket system correctly!
What about flange/fastener bending ? and such long bolts what about thermal length changes ???
How does a slight gasket and/or bolt hole misalignment effect the entire stack ?
Many systems I've also seen use a crazy amount of spring washers (40+)... to maintain loading forces with material creep etc..
Do the normal calculations for spring washers also start breaking down ?.. surely losses from things like friction etc start becoming major factors when stacking so many together.
I am trying to create a list of additional considerations compared to a single gasket bolted system.. can anybody else think of some or have any additional thoughts?
Thanks in advance for any input!
I want to ask about the bolting on industrial hydrogen electrolysers.
These systems can have 150+ cells bolted together with a single bolting system, to create a stack.
Each cell of the stack are sealed with a gasket of some sort. EPDM, Viton, PTFE etc..
Generally a low internal pressure is present say max 1 bar, and temps upto 90°C.
Example image of an industrial stack, check out the crazy bolting!
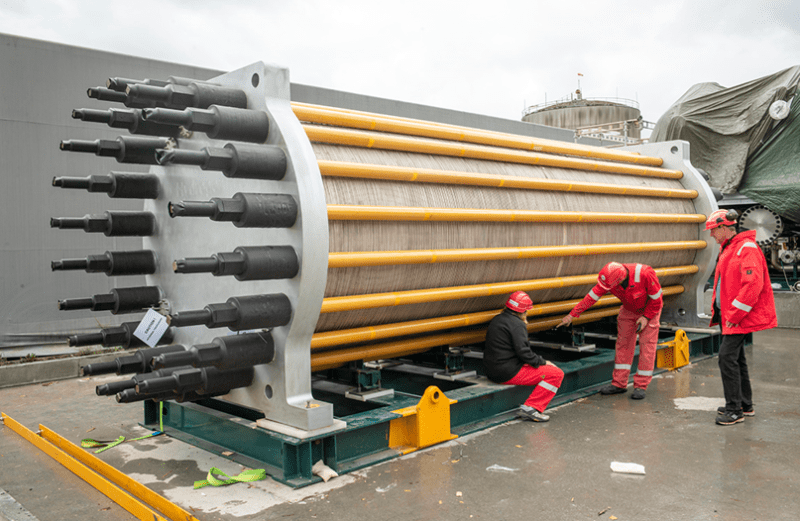
Now normal calculations for a bolted flange joint are for single gasket systems.
How valid is it to use these calculations with a stack of 150 gaskets..
What additional assumptions are we making when stacking 150 of them together.. i.e. does the stress really translate evenly through the whole stack ?
Then how on earth do you load this evenly, many people fail to load a single gasket system correctly!
What about flange/fastener bending ? and such long bolts what about thermal length changes ???
How does a slight gasket and/or bolt hole misalignment effect the entire stack ?
Many systems I've also seen use a crazy amount of spring washers (40+)... to maintain loading forces with material creep etc..
Do the normal calculations for spring washers also start breaking down ?.. surely losses from things like friction etc start becoming major factors when stacking so many together.
I am trying to create a list of additional considerations compared to a single gasket bolted system.. can anybody else think of some or have any additional thoughts?
Thanks in advance for any input!