Helllo all,
I'll post two different questions in a same thread.
-----------------------------------------------------------------------------
Question 1
I have made several fastener connections in a model, through spider RBE3s and the fastener represented by a RBE2. I leave an image so you can see.
The problem is that when I try to extract the loads acting on the element, it's zero in both nodes of the RBE2. I realized that it's because the contribution of both RBEs is cancelled, which is logical. I've tried lots of things to extract these forces but I couldn't do it.
Any experienced FEMAP user could provide a workaround ? Otherwise I'll have to change the RBE2 for CBEAM or CBUSH, but that's something I am trying to avoid because it will be a ton of work.
However, lesson learnt, I won't use RBE3 spider + RBE2 if I want to extract loads.
-----------------------------------------------------------------------------
Question 2
I was performing some post-processing in solid elements, around a hole to be more precise. I had an issue with a high local stress.
A more experienced colleague told me that I was using "Average" for the result output and that I should use (it is what he does) "No average, Centroid Only".
By doing this the stress shown in the solid element passed from 600 [MPa] to around 240 [MPa].
Next, I did the same with plate elements, but the stress (MaxPpal) increased.
My question, therefore, is : How does it work with plate and solid elements ? I mean it seems counterintuitive that by no averaging the results, the output is higher.
Thanks in advance for your time and sharing some knowledge !
Cordially,
EC
I'll post two different questions in a same thread.
-----------------------------------------------------------------------------
Question 1
I have made several fastener connections in a model, through spider RBE3s and the fastener represented by a RBE2. I leave an image so you can see.
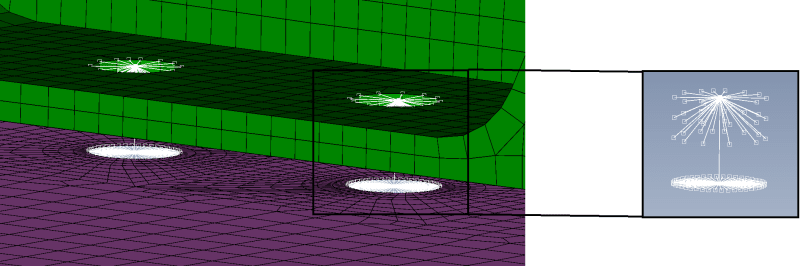
The problem is that when I try to extract the loads acting on the element, it's zero in both nodes of the RBE2. I realized that it's because the contribution of both RBEs is cancelled, which is logical. I've tried lots of things to extract these forces but I couldn't do it.
Any experienced FEMAP user could provide a workaround ? Otherwise I'll have to change the RBE2 for CBEAM or CBUSH, but that's something I am trying to avoid because it will be a ton of work.
However, lesson learnt, I won't use RBE3 spider + RBE2 if I want to extract loads.
-----------------------------------------------------------------------------
Question 2
I was performing some post-processing in solid elements, around a hole to be more precise. I had an issue with a high local stress.
A more experienced colleague told me that I was using "Average" for the result output and that I should use (it is what he does) "No average, Centroid Only".
By doing this the stress shown in the solid element passed from 600 [MPa] to around 240 [MPa].
Next, I did the same with plate elements, but the stress (MaxPpal) increased.
My question, therefore, is : How does it work with plate and solid elements ? I mean it seems counterintuitive that by no averaging the results, the output is higher.
Thanks in advance for your time and sharing some knowledge !
Cordially,
EC