-
1
- #1
Hello there
I usually design steel lug hanger using AISC or EN 1993-1-9_2006 EUROCODE 3.
I have checked that the eurocode or the aisc is sufficient for tension plane failure, single plane failure, double plane failure. The safety factor is sufficient
However when i checked it with 2D 6-dof plate-shell FEA for linear analysis, the von misses is greater that lets say 55%-60% of yield, which the allowable stress load.
Maybe my load pressure is false, i checked the bearing load femap example for 2D, looks fine.
Hope there is someone who already compared the fea lug model with hand calc analysis as examples (book also preffered). any code is alright, AISC, Eurocode3, ASME or Stress Analysis Air force.
Regards
connecting plate by vendor
m70 hanger, recommended plate 50mm thick S355
ultimate load max EC3 is 1663kN, i suppose we have a load between 750kN to 997kN (0.6 Ultimate), and stress still in service allowable condition
I usually design steel lug hanger using AISC or EN 1993-1-9_2006 EUROCODE 3.
I have checked that the eurocode or the aisc is sufficient for tension plane failure, single plane failure, double plane failure. The safety factor is sufficient
However when i checked it with 2D 6-dof plate-shell FEA for linear analysis, the von misses is greater that lets say 55%-60% of yield, which the allowable stress load.
Maybe my load pressure is false, i checked the bearing load femap example for 2D, looks fine.
Hope there is someone who already compared the fea lug model with hand calc analysis as examples (book also preffered). any code is alright, AISC, Eurocode3, ASME or Stress Analysis Air force.
Regards
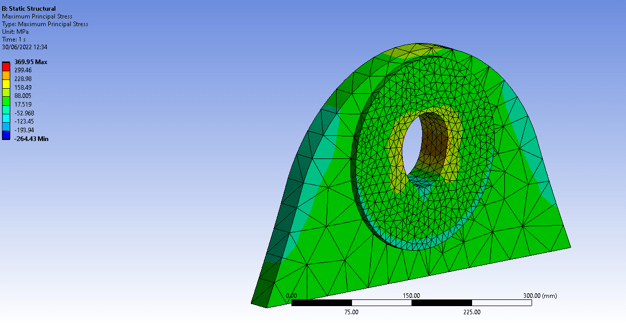
connecting plate by vendor
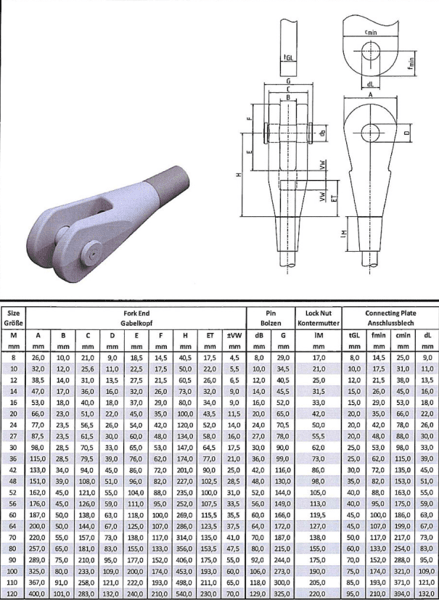
m70 hanger, recommended plate 50mm thick S355
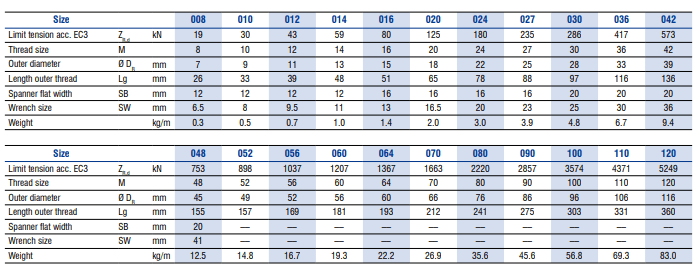
ultimate load max EC3 is 1663kN, i suppose we have a load between 750kN to 997kN (0.6 Ultimate), and stress still in service allowable condition