niccolo_tu
Industrial
Dear all,
I'd like to ask an opinion about a power plant boiler.
The attached picture shows a superheater heat exchanger.
The material is partially ASTM A213 T12 and partially 14CD3 (Afnor standard, should be equivalent to a ASTM A213 T22).
The internal fluid is steam, internal pressure 85 [bar], average inlet temperature 310 [°C], average outlet temperature 460 [°C].
The external fluid are flue gas (whood biomass combustion), average inlet temperature 730 [°C], average outlet temperature 420 [°C], about 20 [%] water content (the rest is CO2, O2, N2. There are traces of HCl and SO2 (about 0.2 [mg/Nm3])) and fly-ashes content. The average flue-gas velocity is about 3.5 [m/s].
As you can see the the external tubes surface is affected by corrosion-erosion-(combination of both?) phenomena.
The white material attached on the external surface are ashes.
I accept any suggestions or advice.
Thanks.
I'd like to ask an opinion about a power plant boiler.
The attached picture shows a superheater heat exchanger.
The material is partially ASTM A213 T12 and partially 14CD3 (Afnor standard, should be equivalent to a ASTM A213 T22).
The internal fluid is steam, internal pressure 85 [bar], average inlet temperature 310 [°C], average outlet temperature 460 [°C].
The external fluid are flue gas (whood biomass combustion), average inlet temperature 730 [°C], average outlet temperature 420 [°C], about 20 [%] water content (the rest is CO2, O2, N2. There are traces of HCl and SO2 (about 0.2 [mg/Nm3])) and fly-ashes content. The average flue-gas velocity is about 3.5 [m/s].
As you can see the the external tubes surface is affected by corrosion-erosion-(combination of both?) phenomena.
The white material attached on the external surface are ashes.
I accept any suggestions or advice.
Thanks.
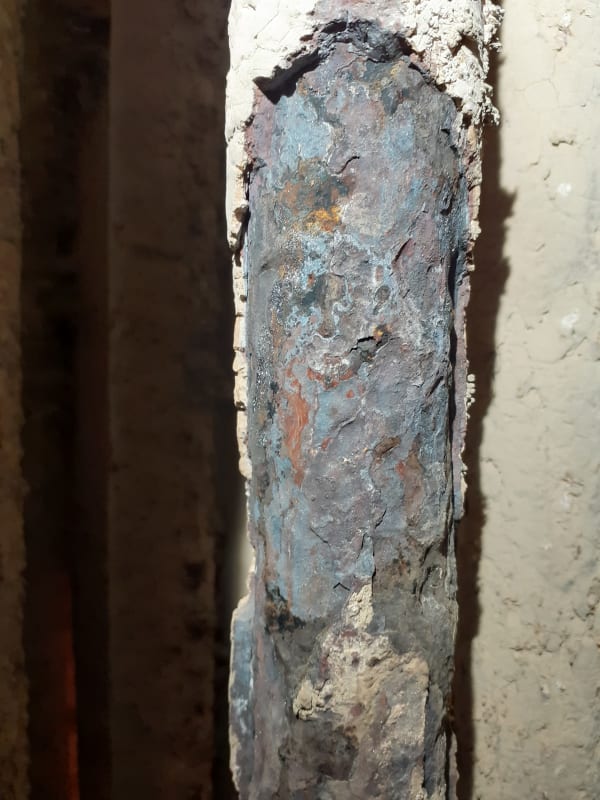
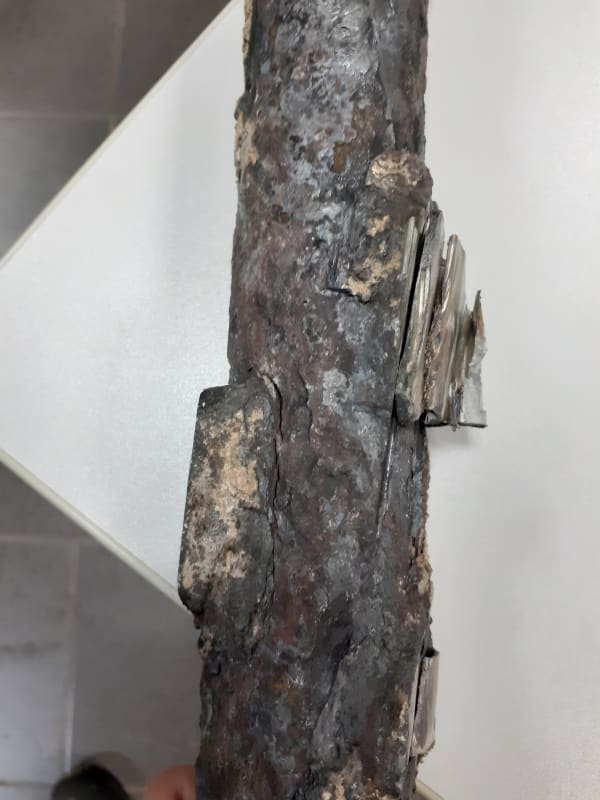
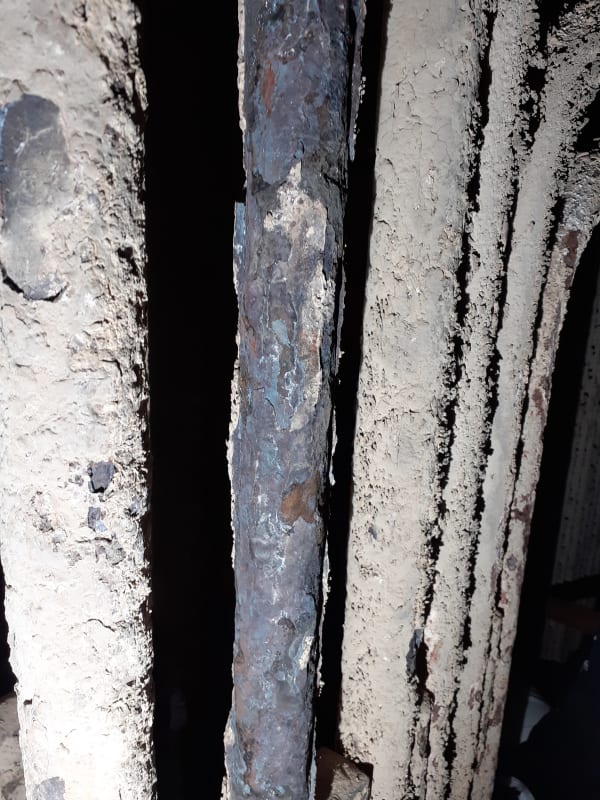
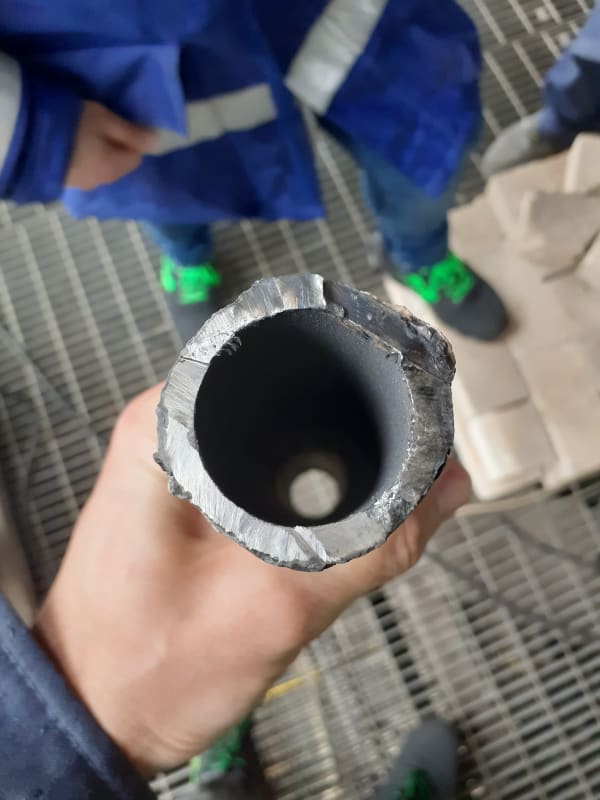
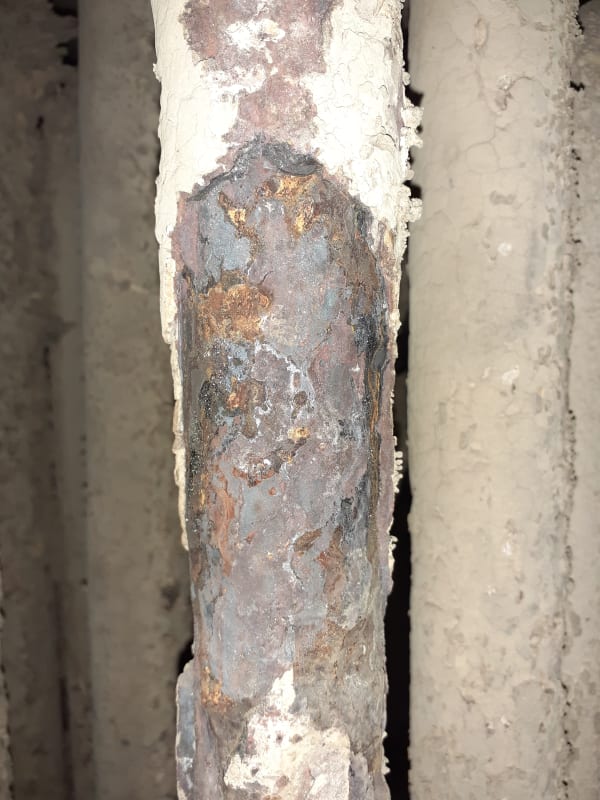
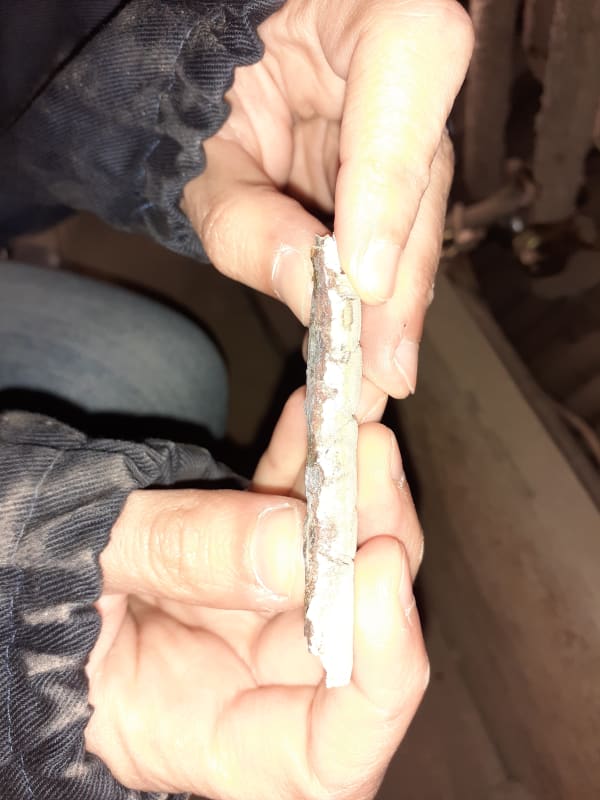
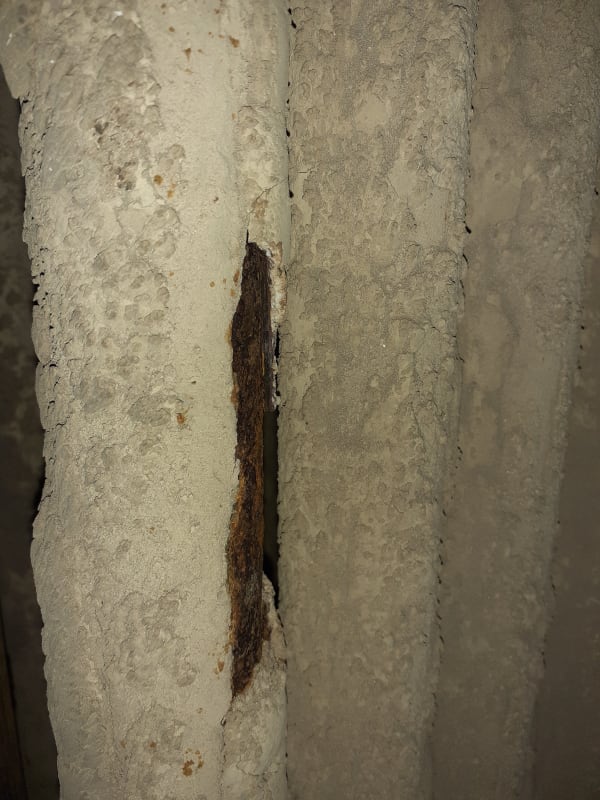