MacMcMacmac
Aerospace
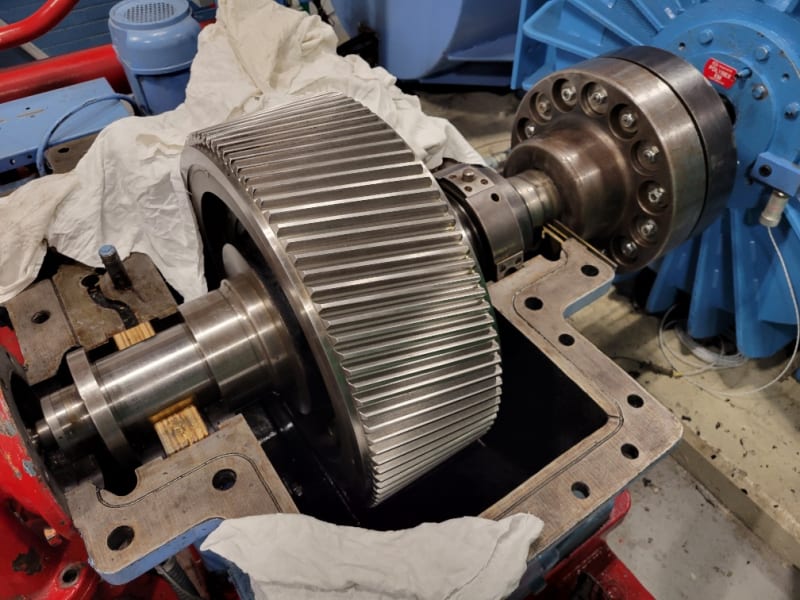
Good Day. We recently received our 1MW motor back from a re-bearing job. The DE bearing burnt up due to a lack of lubrication. It is a double spherical roller bearing that is lubricated through a port on a center groove machined into the periphery of the race. To me at least, it looked as though this bearing was insufficiently packed when it was overhauled last time in 2019. It had intermittent use since then. After investigating the failure, it seemed as though the grease port was also blocked, so it was a double whammy for that bearing. At any rate, we reinstalled the motor to a gearbox last week and were surprised to find our vibration monitor lighting up like a Christmas tree, with axial vibration being the highest. We had an outside expert come in to do some vibration analysis with some higher end gear than we had at our disposal, and he pointed to the gearbox as being the problem. Tear-down revealed nothing more than one worn thrust face. There was also some wear on the far side of the driven exhauster bearing. I am thinking that the motor may not have found its magnetic center before coupling up and there were severe thrust loads put into the gearbox causing the wiping of the thrust face.
Here is the kicker though. When the motor was installed, it became clear that during initial installation, there was so little clearance between the motor mounting holes and the bolts, that one bolt had to be machined in order to get it to pass through the hole. This severely limits the ability to set the motor in any position other than where it is. It has operated like this for decades, so I doubt this has caused the issue. The shafts were laser aligned with a PrufTeknic (sp) Rotalign and there was smiley faces all around.
The motor and gearbox are coupled by a large solid machined pair of hubs with 14 drive pins. The hubs are about 16" o.d., and complete with pins the whole assembly is estimated to be around 440lbs. We noticed that some replacement pins that were fabricated in house weight as much as 10grams less than the older pins. There were also 2 different types of lock nuts on the pins which varied by 5 grams. I do not think that these could be responsible for the vibration issues given the low speeds and weight of the hub. i would like to replace these with a grid coupling, since they are time consuming to link up. I am not sure how tolerant grid couplings are of thrust loads however. The balance condition of these hubs are also unknown. This is a mid 30s era machine, taken as war booty after the WWII. It was apparently installed at the the V2 works.
I noticed during the installation of the coupling drive pins that I was able to insert a large pry bar between the face of the drive and driven hub and move the rotor about 5/16" of an inch axially away from the D.E.. This seems excessive to me. The axial travel of the rotor away from the drive end seems constrained by the D.E. bearing bottoming out in its housing, but the axial travel towards the D.E. seems to be constrained by nothing bu the pins, or the hub faces, which is to say, the inward travel of the N.D.E. bearing has not bottomed out in its housing. i hope that is not too confusing.
The motor was converted from sleeve bearings to roller bearings in about the mid 90s. On the new end covers, the end caps of the bearing housings have an inner lip or "spigot" that I assumed set the position of the bearings, and hence, the shaft in the motor. Upon further inspection, the NDE bearing race of the identical second stage exhauster motor in the train had a gap of about 1/8" of an inch to the raised spigot ring, while the NDE bearing of the repaired motor had a gap of about 1 3/4" between the bearing race and the spigot ring. I honestly don't see what if anything is keeping this rotor from walking axially. The bearings are secured to the shaft with a locking nut and lock washer, and when the rotor is moved manually the whole bearing slides inside the end cover. The repair shop said if the bearing O.D. is on the small side of tolerance, it can have enough give to move in the case. I do not have the expertise to contradict this, but even in small motors there is usually a wave washer of some kind to help keep the rotor where it needs to be.
I have read in another post that motor tend to want to have some thrust into the driven machine, and that if there is not, it can oscillate around magnetic center. This seems somewhat plausible given the symptoms. I cannot think of another reason for high axial vibes. The motor was run uncoupled after the vibration run, and signatures jibed with what the repair shop had taken before shipment. Balancing the rotor was also done as part of the repair.