mechengineer
Mechanical
- Apr 19, 2001
- 268
Hi pressure vessel design enthusiast, experts,
At the location of circumferential joint of spherical head to shell, we can see that the cylinder portion of 250 mm, the small end of 85 mm and the large end is 165 mm. The small end thickness determined by the longitudinal stress [pd/4t] of the cylinder which is same as the stress in the spherical head (hoop stress = longitudinal stress in spherical head = pd/4t).
May we infer that the same is true for the connection of girth flange to shell? The premise is both of shell and flange have to meet the strength requirement itself. That means to use the longintudinal stress to determine g0 of the girth flange rather than the hoope stress [pd/2t] as per ASME VIII-1 Appendix-2. I think that the sloped portion of the shell connected with the spherical head may be a strong example of validation (practical evidence). Just use a girth flange to replace the spherical head.
Very immature idea, I hope experts give pointers. The attractive point to me is able to reduce electrodes consumption by almost 50% as well as for labor of welding work, especially for thicker wall pressure vessels.
At the location of circumferential joint of spherical head to shell, we can see that the cylinder portion of 250 mm, the small end of 85 mm and the large end is 165 mm. The small end thickness determined by the longitudinal stress [pd/4t] of the cylinder which is same as the stress in the spherical head (hoop stress = longitudinal stress in spherical head = pd/4t).
May we infer that the same is true for the connection of girth flange to shell? The premise is both of shell and flange have to meet the strength requirement itself. That means to use the longintudinal stress to determine g0 of the girth flange rather than the hoope stress [pd/2t] as per ASME VIII-1 Appendix-2. I think that the sloped portion of the shell connected with the spherical head may be a strong example of validation (practical evidence). Just use a girth flange to replace the spherical head.
Very immature idea, I hope experts give pointers. The attractive point to me is able to reduce electrodes consumption by almost 50% as well as for labor of welding work, especially for thicker wall pressure vessels.
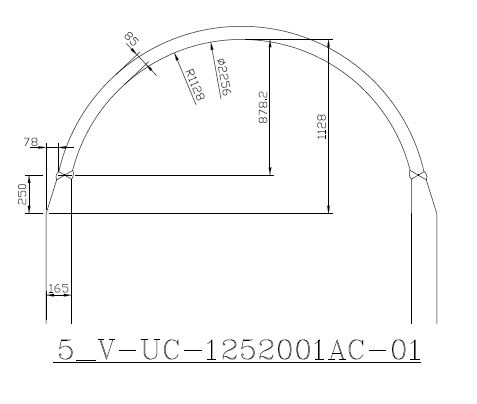