alone_dancer
Mechanical
Hello,
I have a question about the DRF. How to define it for the actual part?
Is the understanding of the two DRFs on the left side of the figure below correct?
My doubts are mainly about the origin and direction of the coordinate system.
Thank you.
I have a question about the DRF. How to define it for the actual part?
Is the understanding of the two DRFs on the left side of the figure below correct?
My doubts are mainly about the origin and direction of the coordinate system.
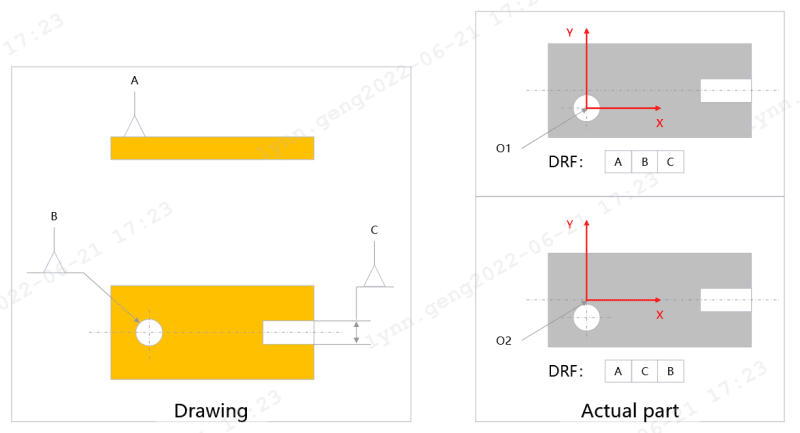
Thank you.