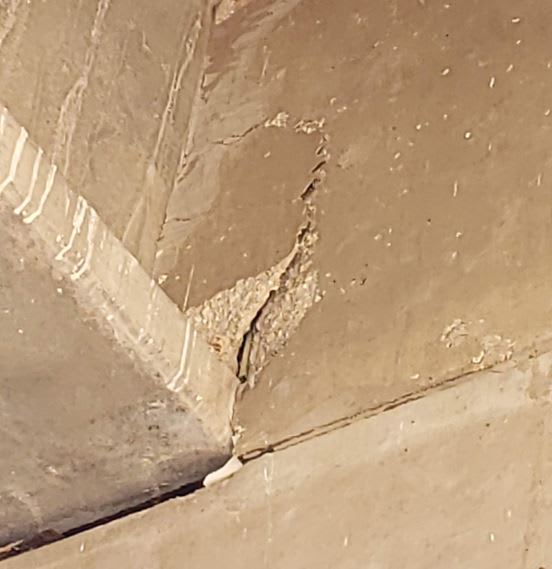
Hello,
I have come across a bridge that has diagonal cracks on the pier diaphragm as shown in the image. The bridge is a prestressed girder bridge. I know there are a number of reasons that could cause this but I have heard this is pretty common on prestressed girder bridges.
Can someone list out a few reasons why this could happen? Girder end rotation is one of the reasons, but I am having a hard time understanding why girder ends would rotate in the first place. Thermal movements are accounted for by the slots in the bearing.